Unterschied zwischen chemischer Vernickelung und galvanischen Beschichtungen
Die galvanischen Beschichtungen (z. B. Verchromung, elektrolytische Vernickelung, Verzinkung, Zink-Nickel) werden unter Verwendung von auf das Werkstück aufgewandtem Gleichstrom abgeschieden, der die Abscheidung des Metalls auf der Oberfläche des zu beschichtenden Werkstücks ermöglicht.
Der aufgewandte Strom neigt dazu, sich auf dem Weg mit dem geringsten Widerstand zu entladen, und folglich ist die Dicke der galvanischen Beschichtung auf den Außenflächen der Werkstücke und an den Kanten größer und auf den inneren Hohlräumen geringer oder bleibt sogar aus, wenn das beschichtete Werkstück komplex ist.
Die chemische Vernickelung ist ein Prozess der Abscheidung einer Nickel-Phosphor-Legierung, der durch eine chemische Redoxreaktion ohne Strom erfolgt. Das Hauptmerkmal besteht darin, alle Oberflächen des Werkstücks mit einer gleichmäßigen und kalibrierten Dicke zu beschichten.
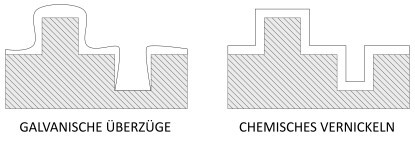
Korrosionsschutzmodus Es gibt zwei Arten von Beschichtungsverhalten, die die Korrosionsbeständigkeit des beschichteten Werkstücks beeinflussen:
- Opferwirkung
- Barrierewirkung
OPFERWIRKUNG
Es handelt sich um den typischen Korrosionsschutz von Beschichtungen auf Zink- und Zink-Nickel-Basis. Zink hat einen geringeren elektrochemischen Potentialwert als Eisen und wird daher opferfähig, indem es zuerst korrodiert und Eisenkorrosion verhindert. Erst wenn sich das Zink fast vollständig aufgelöst hat und Bereiche freigelegt werden, beginnt die Korrosion des Eisens, die schnell fortschreitet. Ein typisches Beispiel für Opferkorrosion ist die Magnesiumanode in Haushaltskesseln, die die Korrosion von Stahl verhindert, da Magnesium opferfähig ist. Ein weiteres Beispiel sind Zink- oder Magnesiumanoden, die an Bootsrümpfen verwendet werden. Aus diesem Grund wird bei der Beurteilung der Korrosionsbeständigkeit von verzinkten Werkstücken die Zeit berücksichtigt, die vor dem Auftreten von weißen Korrosionsprodukten (Zinkoxid) und dem Auftreten von roten Korrosionsprodukten (Eisenoxid) verstrichen ist. Ein Beispiel für eine typische Anforderung (für die Verzinkung) der Korrosionsbeständigkeit nach Exposition gegenüber neutralem Salznebel, gemäß ISO 9227, ist: 96 Stunden ohne das Auftreten von weißer Korrosion und 168 Stunden ohne das Auftreten von roter Korrosion.
BARRIEREWIRKUNG
Die durch das chemische Vernickelungsverfahren abgeschiedene Nickel-Phosphor-Legierung hat ein größeres elektrochemisches Potenzial als Eisen und Aluminium und ist daher gegenüber diesen nicht opferfähig. Es wirkt als Korrosionsschutz, da es eine Barriereschicht erzeugt, die eine Abdichtungswirkung gegenüber äußeren aggressiven Stoffen ausübt. Die Nickel-Phosphor-Legierung weist eine hohe chemische Beständigkeit auf und wird durch neutrale Salzlösungen, insbesondere Niplate 500 mit hohem Phosphorgehalt, kaum korrodiert. Aus diesem Grund können allein durch die Beschichtung Tausende von Stunden Salzsprühnebel ohne Korrosion erreicht werden. Es muss jedoch berücksichtigt werden, dass jede Unvollkommenheit der Beschichtung auch nach wenigen Stunden Salznebel die Korrosion des darunter liegenden Materials verursachen kann. Die Ursachen für solche Unvollkommenheiten können vielfältig sein und zu den wichtigsten gehören:
- Porosität der Beschichtung aufgrund des Vernickelungsprozesses selbst oder aufgrund von Einschlüssen/Defekten im Grundmaterial;
- Oberflächen, die roh belassen wurden und daher durch Ziehfehler und oberflächliche Einschlüsse gekennzeichnet sind;
- Fette, Öle und Pasten, die schwer zu entfernen sind;
- scharfe Kanten und Grate;
Für die chemische Vernickelung ist es daher nicht sinnvoll, einen Grenzwert für das Auftreten von Rotrost festzulegen, der auch nach wenigen Expositionsstunden auftreten kann, wenn die Beschichtung einen kleinen Defekt aufweist. Der große Vorteil der chemischen Vernickelung ist die Fähigkeit, das Substrat auch nach vielen Stunden der Exposition gegenüber Salznebel zu schützen. Es treten nur wenige anfängliche Korrosionspunkte und folglich eine sehr geringe korrodierte Oberfläche auf.
Daher wird in der Regel eine Schutzbewertung nach Einwirkung von Salznebel für einen vom Planer festgelegten Zeitraum vergeben, wie im Folgenden näher erläutert.
Bewertung der Korrosionsbeständigkeit der chemischen Vernickelung Die Korrosionsbeständigkeit chemisch vernickelter Produkte wird üblicherweise durch einen neutralen Salzsprühtest (NSS-Test) nach den folgenden zwei Spezifikationen bewertet:
Norm | Beschreibung |
---|---|
ISO 9227 | Korrosionsprüfungen in künstlichen Atmosphären – Prüfung im Salzsprühnebel |
ASTM B117 | Standard Practice for Operating Salt Spray (Fog) Apparatus |
Nach dem Salzsprühtest wird die Bewertung der Korrosionsbeständigkeit anhand der Spezifikation Uni EN ISO 10289 – Bewertung von Proben und Artefakten, die Korrosionsprüfungen unterzogen wurden, durchgeführt. Letztere vergibt eine Schutzbewertung in Abhängigkeit von der korrodierten Fläche in Bezug auf die dem Salznebel ausgesetzte Fläche, wie in der folgenden Tabelle zusammengefasst:
Fehlerbereich A (%) | Rating |
---|---|
Makellos | 10 |
0 < A ≤ 0,1 | 9 |
0,1 < A ≤ 0,25 | 8 |
0,25 < A ≤ 0,5 | 7 |
0,5 < A ≤ 1 | 6 |
1 < A ≤ 2,5 | 5 |
2,5 < A ≤ 5 | 4 |
5 < A ≤ 10 | 3 |
10 < A ≤ 25 | 2 |
25 < A ≤ 50 | 1 |
50 < A | 0 |
Ein Beispiel für ein Rating ist: Rating 7 nach 500 Stunden Exposition gegenüber neutralem Salznebel ISO 9227.
Normalerweise ist die chemische Vernickelung gut korrosionsbeständig, wenn die geeignete Dicke in Abhängigkeit von der Aggressivität der Umgebung, in der das Bauteil verwendet wird, gewählt wird und wenn die Oberflächen eine gute mechanische Bearbeitung aufweisen. Es reicht von Dicken von 5–10 µm für Umgebungen, die nicht besonders exponiert sind, bis zu 20 µm für moderate Korrosion und bis zu 50 µm für aggressive Umgebungen wie die Meeresumwelt.
Die beste Korrosionsbeständigkeit auf Eisen- und Kupferlegierungen bietet das hochphosphorige chemische Nickel Niplate®500 dank seiner amorphen Struktur mit geringer Porosität auch bei Dicken von wenigen Mikrometern. Chemisches Nickel schafft den besten Korrosionsschutz gegenüber dem Grundmetall, wenn es um Kupferlegierungen geht, insbesondere bei Messing, das häufig für Maschinenteile verwendet wird. Der Elektronegativitätsunterschied zwischen Cu-Zn- und Ni-P-Legierungen ist nahezu gleich Null, was dazu beiträgt, die Aggression des chemisch vernickelten Messingteils zu vermeiden. Die Korrosionsbeständigkeit beträgt in diesem Fall mehr als 1000 Stunden bei neutralem Salznebel NSS nach ISO 9227.
Für Aluminium wird hauptsächlich das Anodisieren verwendet, um Korrosionsbeständigkeit zu verleihen. Wenn zusätzlich zu dieser Eigenschaft eine Gleitfläche mit geringer Rauheit, Verschleißfestigkeit und Leitfähigkeit angestrebt wird, ist die beste Beschichtung Niplate eXtreme. Es handelt sich um eine chemische Nickelbeschichtung, die speziell zur Verbesserung der Korrosionsbeständigkeit von Aluminiumlegierungen entwickelt wurde. Für Legierungen mit hohem Siliziumgehalt, wie z. B. Druckgusslegierungen, empfehlen wir Ihnen, uns zu kontaktieren, damit wir Ihnen die beste Lösung in Abhängigkeit von der Legierung und ihrer Zusammensetzung vorschlagen können.