Eine der Haupteigenschaften der chemischen Vernickelung ist ihre Korrosionsbeständigkeit. Die chemische Vernickelung wird auf mechanischen Metallteilen (Stähle, Aluminium- oder Kupferlegierungen) verwendet, wenn ein Schutz vor Oxidation und Korrosion durch äußere Einflüsse erforderlich ist.
Sie wird beispielsweise zum Schutz von Teilen von Industriemaschinen (Verpackungsmaschinen, Werkzeugmaschinen, Textilmaschinen), verschiedenen mechanischen Vorrichtungen (pneumatische Ventile, Stellantriebe, Armaturen) und im Automobilbereich (Bremskolben, interne Komponenten, Zahnräder) eingesetzt.
Die chemische Vernickelung ermöglicht es, die Korrosionsbeständigkeit durch die chemische Beständigkeit der abgeschiedenen Nickelschicht zu erhöhen. Die Schicht besteht aus einer binären Nickel-Phosphor-Legierungsschicht (NiP) mit Phosphorkonzentrationen von 5 bis 13 %. Diese Legierung weist eine hohe Beständigkeit gegen chemische Aggression auf. Sie wird nicht von neutralen Salzlösungen angegriffen und widersteht gut alkalischen oder leicht sauren Umgebungen. Die chemische Nickelschicht wird nicht von Chemikalien angegriffen, die normalerweise in geschlossenen oder offenen, zivilen, industriellen oder Straßenumgebungen vorkommen.
Die chemische Nickelschicht schützt daher vor Korrosion, da sie als Barriere dient und das Basismaterial von äußeren aggressiven Stoffen isoliert, wodurch korrosive Angriffspunkte verhindert, verzögert oder begrenzt werden. Jeder Punkt der Diskontinuität der Schicht (Defekte, Porosität, Einschlüsse, Risse) kann eine Korrosionsauslösung verursachen.
Die Dicke hat einen großen Einfluss darauf, ob diese Diskontinuitäten vorhanden sind oder nicht. Je dicker die Schicht ist, desto geringer ist die „Porosität“ der Schicht und desto geringer sind die möglichen Auslöser der Korrosion.
Der Einfluss des Grundmaterials auf die Wahl der chemischen Vernickelungsdicke
Die Wahl der richtigen chemischen Vernickelungsdicke für die Korrosionsbeständigkeit hängt vom zu schützenden Grundmaterial ab. Das Korrosionsverhalten variiert je nach Basismaterial, da elektrochemische Faktoren zwischen Basis und Beschichtung ins Spiel kommen.
Neben dem Grundmaterial und der Dicke gibt es viele andere Faktoren, die die Korrosionsbeständigkeit von vernickelten Teilen beeinflussen. Weitere Informationen finden Sie im Artikel Faktoren, die die Korrosionsbeständigkeit der chemischen Vernickelung beeinflussen .
Vernickelungsdicke auf Eisenlegierungen
Handelt es sich bei dem Grundmaterial um eine Eisenlegierung, ist es sehr wichtig, dass die Schicht keine Porosität aufweist. Bei Stählen kann jeder Punkt der Diskontinuität der Schicht eine Korrosion des Grundmaterials in einer aggressiven Umgebung verursachen. Darüber hinaus kann aufgrund des unterschiedlichen Reduktionspotenzials zwischen Nickel und Basismaterial bei diesen Materialien ein Phänomen der galvanischen Korrosion auftreten.
Bei Anwendungen, bei denen das vernickelte Teil mit Wasser, Feuchtigkeit oder aggressiven Substanzen in Kontakt kommen kann, ist es daher notwendig, stets größere Dicken in Abhängigkeit von der Aggressivität der Umgebung vorzusehen. In der folgenden Tabelle sind die empfohlenen Dickenwerte angegeben.
Vernickelungsdicke auf Aluminiumlegierungen
Ein ähnliches Argument lässt sich für Eisenlegierungen anführen, wenn man eine kleine Klarstellung vornimmt. Die Korrosionsbeständigkeit der chemischen Vernickelung auf Aluminium ist kritischer, da sie unter dem Phänomen der Korrosion unter der Schicht leiden kann.
Um dieses Problem zu lösen, haben wir unseren Vorbereitungs- und Aktivierungsprozess für Aluminiumlegierungen optimiert. Dies ermöglicht es uns, eine maximale Korrosionsbeständigkeit zu gewährleisten, sodass wir die chemische Vernickelung auf Sicherheitsaluminiumteile im Automobilsektor (Bremskolben) anwenden, bei denen eine Korrosionsbeständigkeit von 720 Stunden im Salznebel (<5 % korrosiver Bereich) erforderlich ist.
Es wurde eine spezielle chemische Vernickelungsbehandlung entwickelt, um die Korrosionsbeständigkeit von Aluminiumlegierungen zu maximieren: die Niplate eXtreme-Behandlung .
Vernickelungsdicke auf Kupferlegierungen
Bei einem Basismaterial aus Kupferlegierung hingegen hat das Vorhandensein von Porosität nur einen sehr geringen Einfluss auf das Korrosionsverhalten des beschichteten Werkstücks. Dies liegt daran, dass das Grundmaterial und die Schicht ein sehr ähnliches Reduktionspotenzial haben und somit kein galvanisches Drehmoment entsteht. Darüber hinaus weisen Kupferlegierungen eine höhere Korrosionsbeständigkeit auf und sind daher bei Korrosionsauslösung weniger korrosiv.
Kupferlegierungsteile mit chemischer Vernickelung können in der Meeresumwelt auch in Tauchgängen mit begrenzten Nischenstärken (15–20 µm) verwendet werden.
Empfohlene Vernickelungsdicken
Die Wahl der Dicke ist nicht immer einfach und unkompliziert, auch weil die Anwendungen der vernickelten Teile sehr vielfältig sind. Manchmal ist es nur der Feldtest, der es ermöglicht, die richtige Dicke zu definieren.
In der folgenden Tabelle sind Richtwerte für die Dicke der chemischen Vernickelung in Abhängigkeit von der Betriebsbedingung angegeben.
Betriebsbedingung | Beschreibung | Beschichtungsdicke auf Eisen- und Aluminiumlegierungen | Beschichtungsdicke auf Kupferlegierungen |
---|---|---|---|
1 – Leicht | Verwendung in Innenräumen in heißer und trockener Atmosphäre | 8±2 µm | 5±2 µm |
2 – Mäßig schwer | Innenraum, in dem Kondensation auftreten kann. Industrielle Innenräume unter trockenen Bedingungen. | 15±2 µm | 8±2 µm |
3 – Schwer | Verwendung im Freien mit häufigem Benetzen durch Regen, Feuchtigkeit oder Wasser. | 30±3 µm | 15±2 µm |
4 – Extrem schwer | Verwendung im Freien in maritimer Umgebung und unter aggressiven Umgebungsbedingungen mit häufigem Benetzen durch Regen, Feuchtigkeit oder Wasser, das Salze mit neutralem oder leicht alkalischem pH-Wert enthält. | 50±5 µm | 20±2 µm |
Für weitere Informationen oder Beratung über die richtige Dicke der Behandlung, zögern Sie nicht, uns zu kontaktieren.
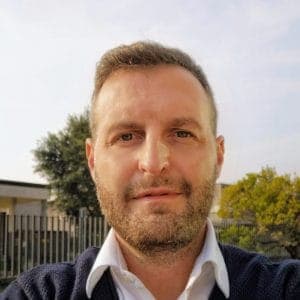