Chemische Vernickelungsbeschichtungen werden aufgrund ihrer Korrosionsbeständigkeit häufig auf mechanische Teile aufgetragen.
Die chemische Nickelschicht weist in der Tat eine hohe chemische Beständigkeit und eine gleichmäßige Dicke auf. Diese Eigenschaften ermöglichen es, eine Barriere zwischen der Basislegierung und der äußeren Umgebung zu schaffen, wodurch die Korrosionsbeständigkeit des Teils erheblich erhöht wird.
Dieser Korrosionsschutzmechanismus unterscheidet sich völlig von anderen Beschichtungen wie Eisenverzinkung. Im Falle der Verzinkung ist die Zinkschicht auf der Oberfläche im Vergleich zum Basismetall opferfähig. Die Zinkschicht hat keine chemische Beständigkeit, sondern korrodiert früher als der Basisstahl. Aber es ist genau diese Eigenschaft, im Vergleich zu Eisen opferfähig zu sein, die es ermöglicht, die Basis vor Korrosion zu schützen.
Die chemische Nickelbeschichtung schützt vor Korrosion, indem sie eine Barriere gegen die äußere Umgebung bildet. Mögliche Korrosionsauslöser sind Bereiche, in denen die Beschichtung nicht kontinuierlich ist.
Die Kontinuität und Integrität der Beschichtung und damit der Grad des Korrosionsschutzes hängen von den Faktoren ab, die die Kontinuität der Schicht beeinträchtigen können. Das Ergebnis wird am meisten durch die vor der chemischen Vernickelung durchgeführten Bearbeitungen beeinflusst.
Die wichtigsten Faktoren sind:
- Beschichtung
- Art des chemischen Nickels (mittlerer, hoher Phosphorgehalt)
- Beschichtungsdicke
- Zu beschichtendes Werkstück
- Metalllegierung des Werkstücks
- Fertigungstechnik (Gießen, Formen, maschinelle Bearbeitung …)
- Werkstückgeometrie (Kanten, Gewinde vorhanden)
- Oberflächengüte und Rauheit (gedrehte, gefräste, geschliffene, rohe, gesprenkelte, geschliffene Oberflächen …)
Verkleidung
Art des chemischen Nickels
Die Art der chemischen Vernickelung, mittlerer chemischer Nickelphosphor oder hoher Phosphor, beeinflusst die Korrosionsbeständigkeit. Die chemische Vernickelung mit hohem Phosphorgehalt weist in der Tat bei gleicher Dicke eine größere Gleichmäßigkeit und Kontinuität der Schicht auf.
Daher haben Teile, die mit chemischem Nickel mit hohem Phosphorgehalt Niplate 500 beschichtet sind, im Allgemeinen ein besseres Korrosionsverhalten als Teile mit chemischem Nickel mit mittlerem Phosphorgehalt Niplate 600.
Beschichtungsdicke
Die Beschichtungsdicke beeinflusst auch die Korrosionsbeständigkeit. Hier gilt, je dicker die Beschichtung, desto größer ist die Abdeckung, Kontinuität und Gleichmäßigkeit der Beschichtung.
Die gewählte Dicke hängt stark von der Anwendung, der Art des chemischen Nickels und vom Grundmaterial des Werkstücks ab. Im Allgemeinen gilt, dass wenn eine hohe Korrosionsbeständigkeit erforderlich ist, die Beschichtungsdicke bei Eisen- oder Aluminiumlegierungsteilen größer als 20 µm sein sollte. Für Kupferlegierungsteile genügt eine Dicke von 10 µm.
Zu beschichtendes Werkstück
Metalllegierung des Werkstücks
Das Korrosionsverhalten hängt stark von der beschichteten Metalllegierung ab. Dies liegt daran, dass an der Schnittstelle zwischen dem Grundmetall und der Beschichtung eine Ionenwanderung (Fretting) zwischen den beiden Metallen entsteht, was zur Korrosionsbeschleunigung führen kann:
- Mit chemischem Nickel beschichtete Kupferlegierungen weisen die beste Korrosionsbeständigkeit auf. Diese Legierungen weisen ein ähnliches Reduktionspotenzial wie die Beschichtung auf, so dass an der Schnittstelle keine galvanische Kopplung entsteht. Beschichtete Kupferlegierungen können selbst bei geringer Schichtdicke (ca. 10 µm) 720 Stunden Salznebel korrosionsfrei überstehen.
- Eisenlegierungen und Aluminiumlegierungen weisen hingegen ein geringeres Reduktionspotenzial auf als Beschichtungen. Dadurch entsteht eine galvanische Kopplung, das die Korrosion an der Schnittstelle beschleunigt. In diesem Fall ist es für eine gute Korrosionsbeständigkeit notwendig, die Dicke der Behandlung (normalerweise größer als 20 µm) zu erhöhen. Die Erhöhung der Dicke ermöglicht es, die Kontinuität der Schicht zu verbessern und somit Korrosionsauslöser zu vermeiden, wodurch das Problem der galvanischen Kopplung zwischen Basis und Beschichtung beseitigt wird.
Fertigungstechnik
Die beste Korrosionsbeständigkeit wird für spezielle mechanische Bearbeitungsprodukte erzielt. Dies liegt daran, dass die mechanische Bearbeitung im Gegensatz zum Schmelzen eine Oberfläche mit besserem Finish, geringerer Rauheit und ohne Porosität gewährleistet.
Die gegossenen Teile, sei es Aluminium oder Gusseisen, weisen auf der Oberfläche Porositäten, Einschlüsse oder andere Defekte auf, die die Kontinuität der Schicht beeinträchtigen und somit das Auslösen von Korrosion ermöglichen.
Werkstückgeometrie
Auch die Geometrie des Werkstücks kann die Korrosionsbeständigkeit beeinflussen. Tatsächlich können scharfe Kanten oder Gewinde in diesen Bereichen die Kontinuität der Beschichtung beeinträchtigen und somit Bereiche mit Korrosionsauslösern schaffen. Um die Korrosionsbeständigkeit zu verbessern, ist es daher ratsam, die Kanten des Teils wo möglich mit Sandstrahlen zu behandeln.
Oberflächenfinish und Rauheit
Die Art der mechanischen Bearbeitung, die zur Herstellung der Oberfläche verwendet wird, und die Rauheit der Oberfläche beeinflussen die Korrosionsbeständigkeit (insbesondere bei Eisen- und Aluminiumlegierungen) erheblich.
Denn wo die Oberflächenrauheit hoch ist (> 1,00 Ra) oder das Material Risse, Grate oder Rillen aufweist, kann es leicht zu Korrosionsauslösern kommen. Dies liegt daran, dass die Beschichtung in diesen Bereichen die Oberfläche nicht kontinuierlich abdeckt.
Schlussfolgerungen
Die Faktoren, die die Korrosionsbeständigkeit beeinflussen, sind zahlreich und es ist schwierig, sie zu zusammenzufassen, auch weil sie miteinander verbunden sind. Die Wahl der Behandlungsspezifikationen hängt auch stark von der Verwendung des Teils ab.
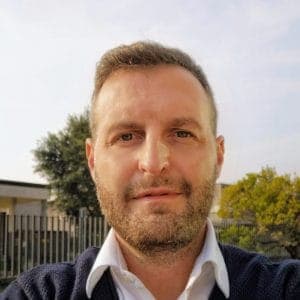