Anodizing (also known as anodic oxidation) is an electrochemical process that produces a compact oxide layer on the metal surface of the treated part. This process uses electric current and its name comes from the fact that the part to be treated is connected to the anode of an electrolytic cell.
Anodizing is the main protective treatment carried out on aluminium . Other metals that can easily be anodized are titanium and magnesium.
Anodizing aluminium
The first Anodizing process, developed in the 1920s-1930s, was based on chromic acid. This coating, called chromic Anodizing, is now only carried out for certain specific sectors such as the military and aeronautics, due to the carcinogenicity of chromium salts.
Currently, the most widespread and most widely used Anodizing process is sulphuric acid-based Anodizing.
The parts to be treated are immersed in a 20 per cent sulphuric acid solution, which acts as an electrolyte. The positive pole is applied to the aluminium piece while the negative pole is connected to a cathode in the solution. When current is applied to the electrolytic cell, oxygen ions develop on the surface of the workpiece, which combine with the aluminium atoms to form a hard, compact layer of aluminium oxide with excellent properties:
- corrosion resistance
- wear resistance
- hardness
- uniformity of thickness
- possibility of coloring with pigments that penetrate the oxide layer
- Dielectric insulation
Oxide layer structure
aluminium oxide, formed by the sulphuric acid Anodizing process, has a columnar honeycomb structure, with hexagonal-shaped cells and a central porosity that extends almost all the way down. The hard Anodizing process forms porosities with a diameter of about 20-40nm and pore-to-pore distance of about 100nm.
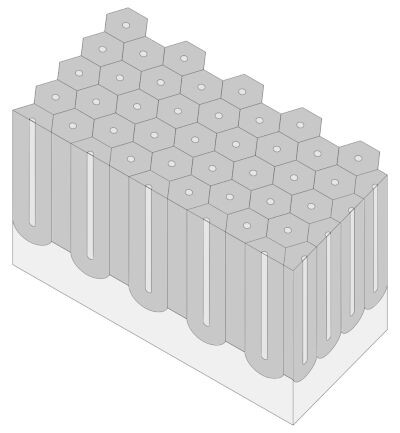
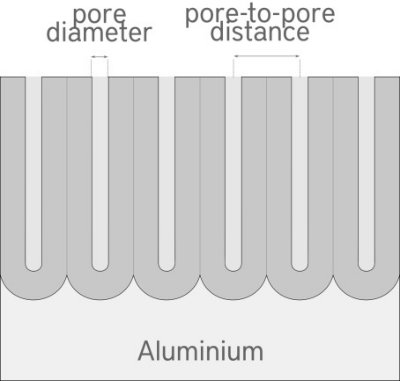
There are two types of Anodizing, with different surface characteristics and different process parameters:
Type of anodizing | Characteristics |
---|---|
Natural or Decorative Anodizing OX-A | Used to provide good resistance to corrosion in non-aggressive environments and moderate resistance to wear and scratches. Used for decorative purposes as it can be colored in a variety of colors. |
Hard anodizing OX-HS - OX-W | Used on precision engineering parts to provide excellent corrosion and wear resistance, high hardness and resistance in aggressive environments. |
Hard Anodizing of aluminium
The term hard Anodizing is used to identify a very hard and compact aluminium oxide coating with greater thicknesses than decorative Anodizing. It is mainly used in precision mechanics on machined parts from solid, extruded, cast and rolled parts in order to increase corrosion resistance, hardness and wear resistance.
Technical reference standards
The technical specifications and international standards relating to hard anodizing are as follows:
Norm / Standard | Title |
---|---|
ISO 10074 | Anodizing of aluminium and its alloys - Specification for hard anodic oxidation coatings on aluminium and its alloys |
MIL-A-8625 | ANODIC COATINGS FOR ALUMINUM & ALUMINUM ALLOYS - Type III: Hard Anodic Coatings |
UNI 7796 | Rivestimenti per ossidazione anodica dell’alluminio e leghe di alluminio - Ossidazione anodica a spessore - Requisiti e istruzioni generali di controllo |
Aesthetic appearance
Hard Anodizing picks up the surface morphology of the part and it is therefore possible to maintain the surface finish of the aluminium even after Anodizing (e.g. polished, satin-finished, brushed, shot-blasted, sandblasted, etc.).
The coating takes on a self-coloring that depends very much on the aluminium alloy used and can vary between grey, dark grey and brown. After treatment, the surface can be pigmented with black, blue or red dye. These pigments penetrate into the Anodizing layer, coloring it. As the base color of the anodized layer is a dark shade, unlike natural Anodizing treatments, hard Anodizing treatments take on deep black, dark blue and dark red colors.
The thickness influences the coating becoming darker as the thickness increases. Alloys containing a lot of copper acquire a bronze appearance and alloys containing a lot of silicon (>12%) may have an uneven coloring. Hard Anodizing, which is dark in tone, lends itself to being colored with dark, opaque colors and black is usually chosen, both for its excellent appearance and to even out the color in the presence of different alloys.
Anodizable aluminium alloys
All aluminium alloys are Anodizable, with some minor exceptions. The greatest difficulties are encountered with alloys that contain elements other than aluminium in high quantities, as it is only the aluminium that contributes to forming the oxide layer. As a result, alloys containing high amounts of copper, such as those in the 2000 series, cannot achieve high thicknesses and the oxide layer will be slightly less compact and less resistant to corrosion and wear. Alloys containing silicon in amounts greater than 12% may exhibit lower coating thickness and uniformity resulting in lower resistance to corrosion, wear and sometimes uneven color.
Anodizing thickness
A special feature of Anodizing is the possibility of coating parts with a uniform, calibrated thickness on almost all surfaces. An exception may be small diameter and very deep holes, for which the penetration capacity of the coating must be individually assessed.
The standard thickness of hard Anodizing is 30-50µm, but lesser or greater thicknesses can be chosen depending on specific requirements. With very tight tolerances, one tends to decrease the Anodizing thickness and/or define a tighter tolerance such as 30±5µm.
Dimensional growth
The treatment thickness increases by 50% outside and 50% inside the surface of the aluminium piece. The radial dimensional increase is therefore equal to half the treatment thickness.
Corrosion resistance
Hard Anodizing has a higher resistance to corrosion than decorative Anodizing, due to the higher thickness and compactness of the oxide layer. This resistance can be affected by porosity in the coating, which is the first corrosion trigger. In order to increase corrosion resistance, a treatment is carried out after Anodizing, known as sealing. There are various types of sealing and the two most widely used industrially and internationally recognized are:
- hot seating: immersion in water at a temperature of about 95°C, which allows surface hydration of the aluminium oxide layer and closes the porosity, thus allowing better resistance to corrosion.
- cold sealing: immersion in a nickel fluoride solution at room temperature. The nickel salts penetrate the porosity of the coating, improving corrosion resistance.
Although hot sealing is energy-intensive because it must be maintained at 95°C, it is increasingly used, to the detriment of nickel salts, which are carcinogenic and can cause skin allergies. In the food industry, for example, nickel-based sealing cannot be used.
Anodizing resists corrosion very well in contact with alcohols, hydrocarbons and neutral solutions. Acidic or basic solutions dissolve the aluminium oxide, thus negating the barrier effect of corrosion protection. The dissolution rate of the Anodizing layer is proportional to the acidity or basicity of the solution and higher in the case of basic solutions.
OX-W Hard anodizing is a treatment specially developed to increase the already excellent corrosion resistance of hard Anodizing. On some alloys, it allows up to 1000 hours of exposure to neutral salt spray according to ISO 9227, without the appearance of corrosion. OX-W is also suitable for protecting alloys with a high silicon content, which may have difficulties with the standard Anodizing process.
Hardness, density and wear resistance
Hard Anodizing has a high hardness, which varies according to the aluminium alloy used.
The ISO 10074 specification defines the minimum hardness of certain alloys. The hardness is measured according to ISO 4516 on a layer with a thickness between 25-50µm and a load of 50g HV 0.05.
Alloy | Vickers hardness |
---|---|
wrought alloys | 400 HV |
2000 series | 250 HV |
5000 series with Mg >2% | 300 HV |
7000 series | 300 HV |
Casting alloys with Cu <2% and/or Si <8% | 250 HV |
The density, measured in accordance with ISO 2106 on a coating of 50µm ± 5µm without sealing, must have the following minimum values:
Alloy | min. surface density |
---|---|
wrought alloys | 1100 mg/dm2 |
2000 series | 950 mg/dm2 |
5000 series with Mg >2% | 950 mg/dm2 |
7000 series | 950 mg/dm2 |
Casting alloys with Cu <2% and/or Si <8% | 950 mg/dm2 |
The high hardness and compactness of the oxide layer and the columnar structure allow hard Anodizing to achieve a high wear resistance, higher than electroless nickel plating and comparable to hard chrome plating in thickness. The Taber Abraser is a test that determines the wear of sliding coatings on abrasive wheels. According to ISO 10074, after 10,000 cycles, the mass loss must be less than the following values:
Alloy | max. loss in mass |
---|---|
wrought alloys | 15 mg |
2000 series | 35 mg |
5000 series with Mg >2% | 25 mg |
7000 series | 25 mg |
Casting alloys with Cu <2% and/or Si <8% | - |
Roughness
Hard Anodizing contributes to a slight increase in surface roughness and is most noticeable on surfaces with low machining roughness.
OX-W hard Anodizing has the characteristic of limiting the increase in surface roughness. By using specific aluminium alloys and defining the right operating parameters, it is possible to keep the final roughness below 0.5 Ra.
Food contact
The standard “EN 14392 Requirements for anodized products for use in contact with foodstuff” specifies the requirements for Anodizing treatments on aluminium parts intended for contact with foodstuffs.
The treatments carried out by Durox srl comply with EN 14392 if the following requirements are met:
- The chemical composition of the aluminium alloys of the parts to be anodized must comply with the requirements of EN 601 or EN 602, as far as applicable.
- The Anodizing treatments must undergo the sealing phase which must be expressly requested.