The hard anodizing of aluminum is a process that allows creating a layer of aluminum oxide on the material’s surface with hardness and wear resistance properties superior to those of natural or architectural anodizing.
This is because the hard anodizing layer has a greater thickness and is obtained using different process parameters, such as the electrolyte temperature, which in hard anodizing is approximately 0°C, compared to the 20°C of architectural anodizing. In this way, a hard and wear-resistant coating is obtained, suitable for various types of applications.
Hardness
As previously mentioned, hard anodizing exhibits high hardness, which depends on the aluminum alloy used. Generally, the hardness of hard anodizing treatments ranges from 280 to 500 HV, depending on the chosen alloy. For example, aluminum alloys of the 6000 series are particularly suitable for achieving high hardness hard anodizing layers, while alloys of the 2000 series, due to their copper content, attain lower hardness values, around 280 HV. Alloys of the 7000 series fall in between and can reach a hardness of about 350 HV.
Wear resistance
The wear resistance of hard anodizing coatings is a property closely related to the hardness of the treatment. The higher the hardness, the greater the wear resistance. To measure the wear resistance of hard anodizing coatings, the Taber Abraser abrasion resistance test is commonly used. This test involves subjecting a specimen to abrasion by rubbing it with abrasive wheels. Abrasion resistance is calculated based on the weight loss of the specimen before and after the test, which consists of 10,000 cycles of abrasion.
Based on the results obtained with the Taber Abraser test, aluminum alloys of the 6000 series exhibit the highest abrasion resistances, followed by alloys of the 7000 series. Conversely, alloys of the 2000 series show the lowest wear resistances. However, it is important to emphasize that the wear resistance of hard anodizing coatings is generally very high, surpassing that of steel alloys and chemical nickel plating, and comparable to that of hard chrome.
Applications for wear resistance
In addition to providing high corrosion resistance, hard anodizing treatments are used to increase the wear resistance of aluminum alloys.
In the automotive sector, for example, hard anodizing is often applied to mechanical components such as valve bodies, stems, and floaters, which may undergo friction and abrasion during use. Thanks to the hardness and wear resistance of the anodized surface, these components have greater durability. In the bicycle industry, hard anodizing is used, for instance, on chainrings to resist abrasion caused by the chain passing over them. Moreover, in the field of industrial machinery, hard anodizing is frequently applied to transfer rollers in printing machines or packaging machines to reduce wear caused by friction with paper or other materials. Also, in the textile sector, various parts are treated with hard anodizing to resist wear from rubbing against other parts or textile fibers.
Conclusions
In summary, hard anodizing is a surface treatment that provides aluminum alloys with superior hardness and wear resistance compared to natural or architectural anodizing. The hardness of hard anodizing coatings varies depending on the aluminum alloy used but generally falls between 280 and 500 HV. Wear resistance is measured using the Taber Abraser abrasion resistance test and also depends on the chosen alloy. Typically, alloys of the 6000 and 7000 series exhibit higher abrasion resistance, while those of the 2000 series have lower wear resistance. Nonetheless, it’s crucial to note that the wear resistance of hard anodizing coatings is generally very high and surpasses that of steel alloys and chemical nickel plating.
Hard anodizing finds application across various industrial sectors including automotive, bicycle manufacturing, industrial machinery, and textiles, to increase the durability and wear resistance of components subject to friction and abrasion. Thus, hard anodizing serves as an effective solution for enhancing the performance and lifespan of many products.
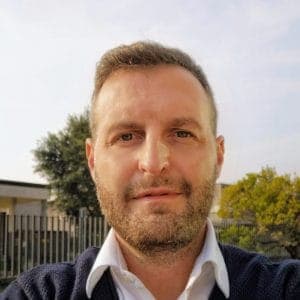