After the fall of the Berlin Wall, several Russian technologies were investigated by the western world in the early 90s to assess their industrial applicability. These technologies came from Russian space and military research. Among the surface treatments for metals, electrolytic treatments called Plasma Electrolytic Oxidation PEO, also known as Micro-Arc Oxidation MAO, gained a certain amount of interest, they made it possible to create an extremely hard and compact oxide layer on aluminium , magnesium and titanium using high-voltage current.
Micron Srl set up the first CE machine derived from the Russian model in collaboration with Keronite and began an R&D programme to improve the characteristics of the oxide layer created using different currents varying in power and frequency. Micron and Keronite parted ways at some point and each continued the R&D programme on their own.
The PEO treatment process
PEO is based on the principle of applying a high-voltage current, periodically reversed, to an Anodizable metal part immersed in a special solution called electrolyte. In this way, an oxide layer is created and at the same time the metal is melted by discharges due to the high voltage passing through it. The workpiece immersed in the electrolyte becomes covered with countless small electrical discharges or ‘micro-arcs’ that envelop the workpiece, illuminating it while causing the ceramic layer to form.
The result is the formation of a mineralized oxide layer by fusion, the hardness of which is equal to the hardness of the metal’s original oxide. On pure aluminium , hardnesses similar to those of alumina Al2O3 are reached at around 2000 HV, on titanium around 1000 HV and on magnesium around 600 HV. On commonly used aluminium alloys, due to the different metals present in the alloy, hardnesses between 1200 HV and 1600 HV can be achieved.
Evolution of PEO treatment
Continuous research and development has led to an evolution and refinement of the micro-spark or micro-arc process, with better distribution and refinement of the electrolytic plasma discharges, improving surface characteristics and allowing the ceramic coating to be used without polishing and with better thickness uniformity.
The electrolytes used are slightly alkaline solutions without the addition of heavy metals or hazardous chemicals, making the process environmentally friendly and safe for the health of the operators. For each of the three metals, Al, Mg, Ti, different electrolytes and machine settings are used to obtain the ceramic surface layer.
Micron has developed and evolved the Plasma Electrolytic Oxidation PEO treatment on magnesium and aluminium in collaboration with a British company. The use of magnesium metal and its alloys has always been limited by its poor resistance to corrosion, despite its light weight of 1.8 kg/dm3, its excellent machinability and the possibility of being die-cast.
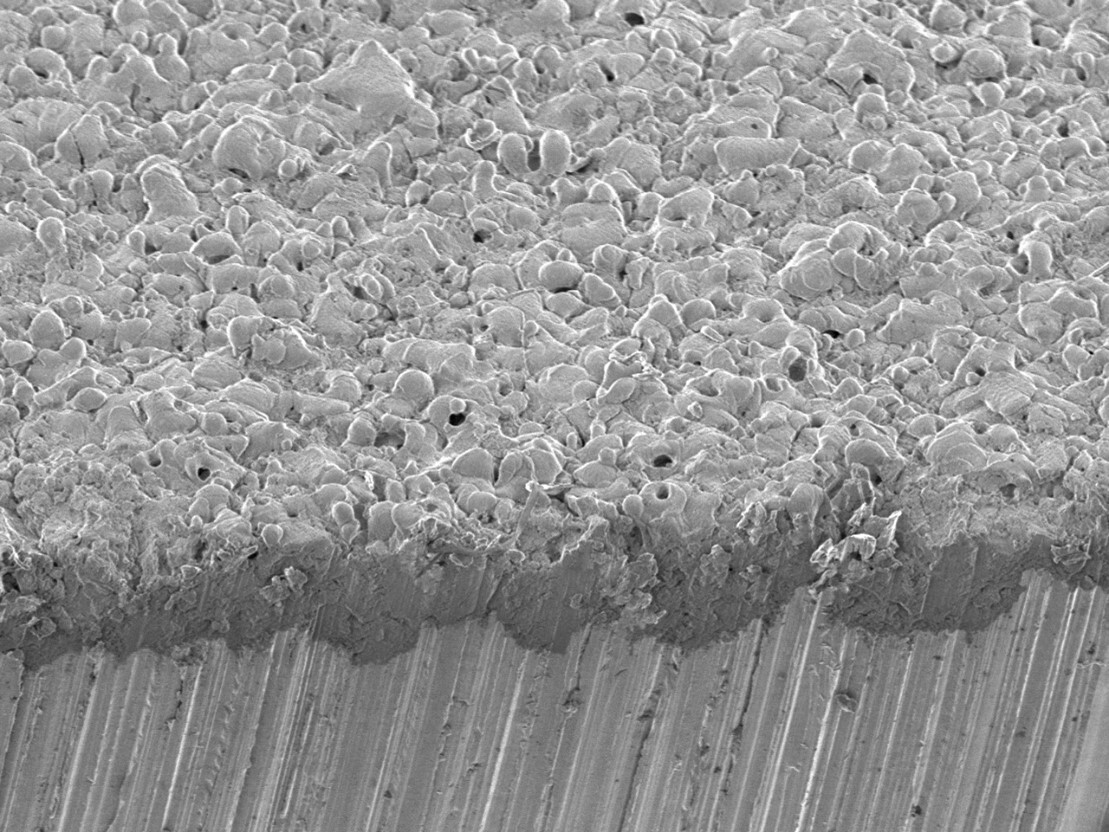
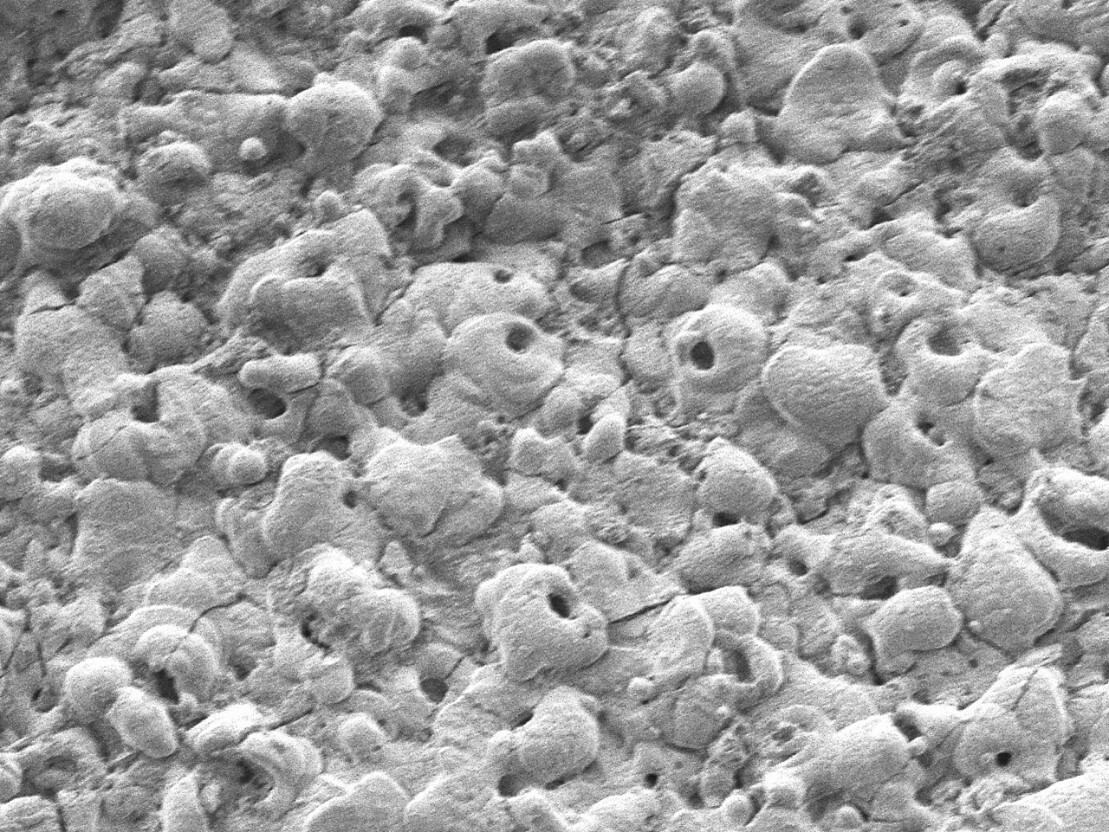
Features of PEO OX-UHA coating on Magnesium
Before the advent of PEO, corrosion protection on magnesium relied on HAE treatments, classic anodizing, or chromating with Cr6, with less than excellent results. With PEO, the ceramic layer, composed mainly of mixed magnesium and aluminium oxides, is very hard (500HV) and compact, which greatly increases corrosion resistance.
An important feature is also its surface structure, which gives excellent adhesion to subsequent impregnation or painting treatments carried out to further increase corrosion resistance.
They can be treated with PEO OX-UHA all common magnesium alloys, with thicknesses usually between 5µm and 20µm. PEO provides excellent corrosion resistance even at low coating thicknesses, due to its compactness and adhesion. PEO transforms the magnesium surface into magnesium oxide, without causing any dimensional growth due to the coating.
The hardness of the coating varies depending on the alloy used and is usually in the range of 400 to 600 HV, values far higher than any other magnesium anodizing treatment. The high hardness thus increases resistance to wear, impacts and scratches.
Both the process and the coating are environmentally friendly as there are no toxic or carcinogenic chemicals present. PEO is the main alternative treatment to chromating, which is being used less and less due to problems with hexavalent chromium. PEO treatment complies with the REACH regulation and the RoHS directive as there are no substances with restrictions of use above the maximum tolerated concentrations and no SVHC are present in quantities above 0.1% by weight.