Difference between electroless Nickel Plating and Electroplated Coatings
Electroplated coatings (such as chrome plating, electroless nickel plating, zinc plating, zinc-nickel plating) are deposited by applying direct current to the part, which allows the metal to be deposited on the surface of the part to be coated.
The applied current tends to discharge following the path of least resistance, resulting in thicker electroplated coatings on the external surfaces and edges of the parts and thinner or even absent coatings on the internal cavities. On the other hand, electroless nickel plating is a process of depositing a nickel-phosphorus alloy through a chemical oxidation-reduction reaction, without the use of current. Its main characteristic is to coat all surfaces of the part with a uniform and calibrated thickness.
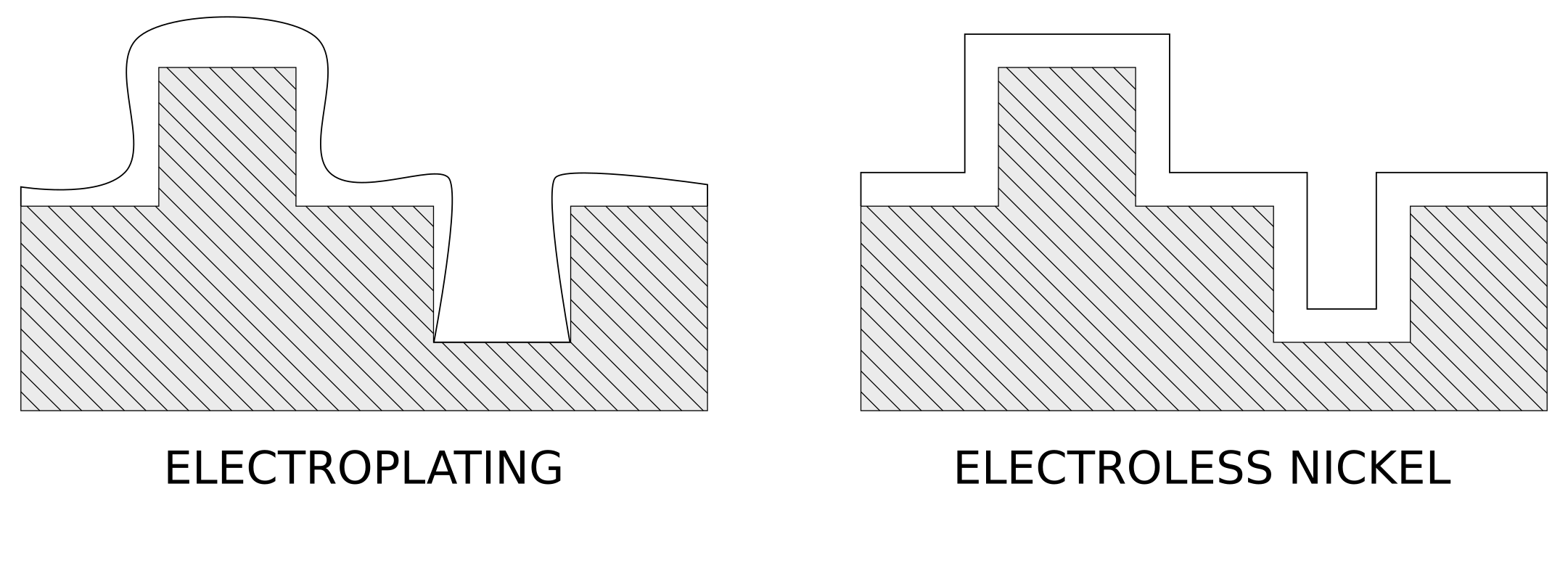
Methods of corrosion protection There are two types of coating behavior that influence the corrosion resistance of the coated part:
- Sacrificial effect
- Barrier effect
SACRIFICIAL EFFECT
This is the typical corrosion protection of zinc-based and zinc-nickel coatings. Zinc has a lower electrochemical potential than iron and therefore becomes sacrificial by corroding first and preventing the corrosion of iron. Only when the zinc is almost completely dissolved, leaving uncovered areas, will the corrosion of iron begin, which will progress rapidly. A typical example of sacrificial corrosion is the magnesium anode inserted in domestic boilers, which prevents the corrosion of steel as magnesium is sacrificial. Another example is the use of zinc or magnesium anodes on boat hulls. For this reason, to evaluate the corrosion resistance of zinc-coated parts, the time elapsed before the appearance of white corrosion products (zinc oxide) and the appearance of red corrosion products (iron oxide) is considered. An example of a typical requirement (for zinc plating) for corrosion resistance after exposure to neutral salt spray according to ISO 9227 is: 96 hours without the appearance of white corrosion and 168 hours without the appearance of red corrosion.
BARRIER EFFECT
The nickel-phosphorus alloy deposited by the electroless nickel plating process has a higher electrochemical potential than iron and aluminum and is therefore not sacrificial compared to them. It acts as a corrosion protection by creating a barrier layer that provides a waterproofing effect against external aggressive agents. The nickel-phosphorus alloy has high chemical resistance and is hardly corroded by neutral saline solutions, especially Niplate 500 high phosphorus. For this reason, considering only the coating, thousands of hours of exposure to salt spray can be achieved without corrosion. However, it should be noted that any imperfection in the coating can generate corrosion of the underlying material, even after a few hours of exposure to salt spray. The causes of such imperfections can be multiple, and among the main ones, we find:
- Porosity of the coating due to the nickel plating process itself or to inclusions/defects in the base material;
- Rough surfaces characterized by drawing defects and surface inclusions;
- Difficult-to-remove greases, oils, and pastes;
- Sharp edges and burrs.
For electroless nickel plating, it does not make sense to assign a limit for the appearance of red rust, which can appear even after a few hours of exposure where the coating has a small defect. The great advantage of electroless nickel plating is the ability to maintain the substrate protected even after many hours of exposure to salt spray, showing only a few initial corrosion pits and consequently a very low corroded surface area. A protection rating is usually assigned after exposure to salt spray for a certain number of hours decided by the designer, as detailed below.
Evaluation of corrosion resistance of electroless nickel plating The corrosion resistance of products coated with electroless nickel plating is commonly evaluated through neutral salt spray (NSS) tests according to the following two specifications:
Specification | Description |
---|---|
ISO 9227 | Corrosion tests in artificial atmospheres - Salt spray tests |
ASTM B117 | Standard Practice for Operating Salt Spray (Fog) Apparatus |
Following the salt spray test, the evaluation of corrosion resistance is carried out using the UNI EN ISO 10289 specification - “Evaluation of samples and products subjected to corrosion tests”. This specification assigns a protection rating based on the corroded area compared to the area exposed to salt spray, as summarized in the following table:
Area of defects A (%) | Rating |
---|---|
No defects | 10 |
0 < A ≤ 0,1 | 9 |
0,1 < A ≤ 0,25 | 8 |
0,25 < A ≤ 0,5 | 7 |
0,5 < A ≤ 1 | 6 |
1 < A ≤ 2,5 | 5 |
2,5 < A ≤ 5 | 4 |
5 < A ≤ 10 | 3 |
10 < A ≤ 25 | 2 |
25 < A ≤ 50 | 1 |
50 < A | 0 |
An example of a rating is: Rating 7 after 500 hours of exposure to neutral salt spray ISO 9227.
Electroless nickel plating typically provides good resistance to corrosion when the appropriate thickness is selected based on the aggressiveness of the environment in which the component is used and when surfaces have a good mechanical finish. Thicknesses range from 5-10 µm for environments that are not particularly exposed, to 20 µm for moderate corrosion, and up to 50 µm for aggressive environments such as marine environments.
The best corrosion resistance for iron and copper alloys is provided by high-phosphorus electroless nickel Niplate®500 due to its amorphous structure with low porosity, even at thicknesses of a few microns. Electroless nickel provides the best protection against corrosion towards the base metal when it comes to copper alloys, especially with brass, which is widely used for mechanical parts. The difference in elettronegatività between Cu-Zn and Ni-P alloys is almost negligible, which helps to avoid the attack of chemically nickel-plated brass pieces. The corrosion resistance in this case exceeds 1000 hours in neutral salt spray NSS according to ISO 9227.
For aluminum, the treatment predominantly used to confer resistance to corrosion is anodizing. If in addition to this characteristic, a smooth surface with low roughness, wear resistance, and conductivity is desired, the best coating is Niplate eXtreme. This is a Electroless nickel coating specifically designed to improve the corrosion resistance of aluminum alloys. For alloys with a high silicon content, such as die-casting alloys, we recommend contacting us to propose the best solution based on the alloy and its composition.