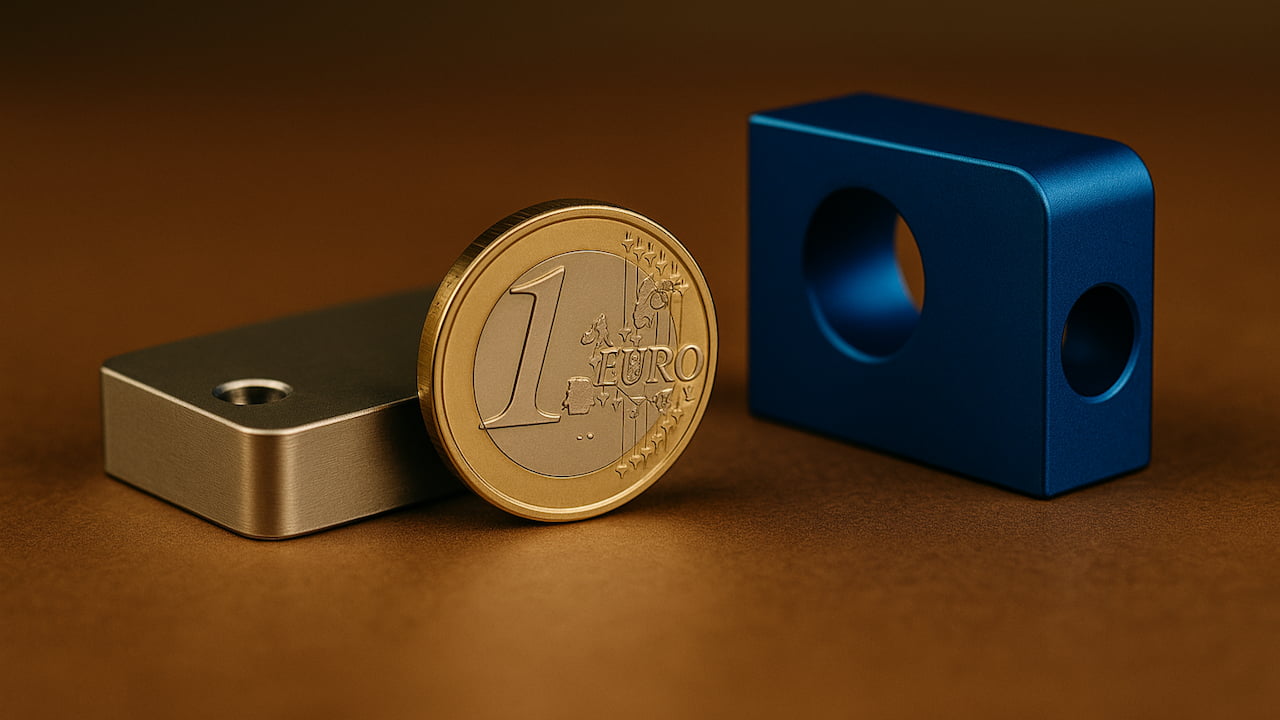
The Cost of Electroless Nickel Plating and Anodizing: What Really Affects the Price?
One of the most common questions we receive from those approaching a technical surface treatment for the first time is:
“How much does it cost per kilo?”
Whether we’re talking about electroless nickel plating or anodizing, the correct answer is: it depends.