La anodización (también llamada oxidación anódica) es un proceso electroquímico que permite obtener una capa compacta de óxido sobre la superficie metálica de la pieza tratada. Este proceso utiliza la corriente eléctrica y su nombre deriva del hecho de que la pieza a tratar está conectada al ánodo de una celda electrolítica.
La anodización es el principal tratamiento protector realizado sobre aluminio. Otros metales que se pueden anodizar fácilmente son el titanio y el magnesio.
Anodización del aluminio
El primer proceso de anodización, desarrollado en la década 1920-1930, se hacía a base de ácido crómico. Este recubrimiento, denominado anodización crómica, se realiza ahora solo para algunos sectores específicos como el militar y el aeronáutico, debido a la carcinogenicidad de las sales de cromo.
Actualmente, el proceso de anodización más común y más utilizado es el que se realiza a base de ácido sulfúrico.
Las piezas que se van a tratar se sumergen en una solución de ácido sulfúrico al 20 % que actúa como electrolito. El polo positivo se aplica a la pieza de aluminio, mientras que el polo negativo se conecta a un cátodo presente en la solución. Aplicando corriente a la celda electrolítica se generan iones de oxígeno en la superficie de la pieza por tratar que, al combinarse con los átomos de aluminio, forman una capa dura y compacta de óxido de aluminio con excelentes características de:
- Resistencia a la corrosión
- Resistencia al desgaste
- Dureza
- Uniformidad de espesor
- Posibilidad de coloración con pigmentos que penetran en la capa de óxido
- Aislamiento dieléctrico
Estructura de la capa de óxido
El óxido de aluminio, formado mediante el proceso de anodización en ácido sulfúrico, tiene una estructura columnar en panal, con celdas de forma hexagonal y con una porosidad central que se extiende a casi toda la profundidad. El proceso de anodización dura forma una porosidad de un diámetro de aproximadamente 20-40 nm y una distancia entre poros de aproximadamente 100 nm.
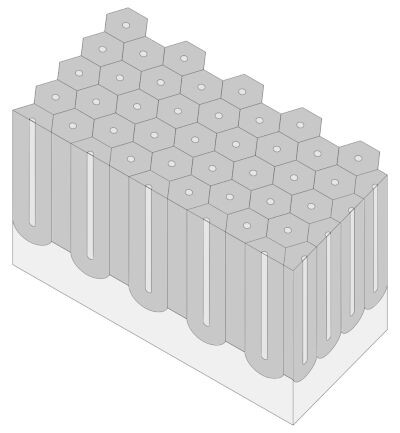
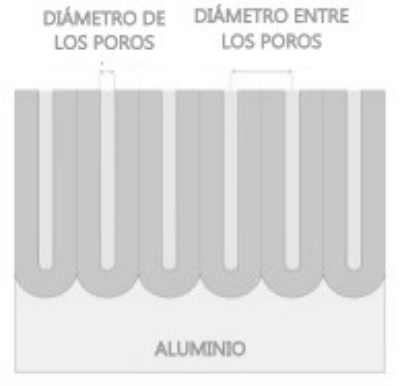
Hay dos tipos de anodización, con diferentes características superficiales y diferentes parámetros de proceso:
Tipo de anodización | Características |
---|---|
Anodización natural o decorativa OX-A | Se utiliza para dar una buena resistencia a la corrosión en entornos no agresivos y una discreta resistencia al desgaste y los arañazos. Se utiliza en el ámbito decorativo, ya que es compatible con múltiples opciones de coloración. |
Anodización dura OX-HS - OX-W | Se utiliza en piezas mecánicas de precisión para conferir una excelente resistencia a la corrosión y el desgaste, así como una elevada dureza y resistencia en ambientes agresivos. |
Anodización dura del aluminio
Con el término anodización dura se identifica un recubrimiento de óxido de aluminio muy duro y compacto, con espesores mayores que la anodización decorativa. Se utiliza sobre todo en la mecánica de precisión en piezas mecanizadas a partir de un bloque de material en bruto, extruidas, fundidas, fundidas a presión y laminadas con el fin de aumentar la resistencia a la corrosión, la dureza y la resistencia al desgaste.
Normas técnicas de referencia
Las normas técnicas y los estándares internacionales relacionados con la anodización dura son las siguientes:
Norma / Estándar | Título |
---|---|
ISO 10074 | Anodizing of Aluminium and its alloys - Specification for hard anodic oxidation coatings on Aluminium and its alloys |
MIL-A-8625 | ANODIC COATINGS FOR ALUMINUM & ALUMINUM ALLOYS - Type III: Hard Anodic Coatings |
UNI 7796 | Recubrimientos por oxidación anódica del aluminio y aleaciones de aluminio - Oxidación anódica de espesor - Requisitos e instrucciones generales de control |
Aspecto estético
La anodización dura replica la morfología superficial de la pieza y, por lo tanto, es posible mantener los acabados superficiales del aluminio incluso después de la anodización (por ejemplo, brillante, satinado, cepillado, «shot peening», granallado, arenado, etc.)
El recubrimiento adquiere una autocoloración que depende en gran medida de la aleación de aluminio utilizada y puede variar entre gris, gris oscuro y marrón. Después del tratamiento, la superficie puede pigmentarse con colorante negro, azul o rojo. Estos pigmentos penetran en el interior de la capa de anodización coloreándola. Dado que el color base de la capa anodizada es de tono oscuro, a diferencia de los tratamientos de anodización natural, los tratamientos de anodización dura adquieren un color negro profundo, azul oscuro y rojo oscuro. El espesor influye haciendo que el recubrimiento se vuelva más oscuro a medida que aumenta el espesor. Las aleaciones que contienen mucho cobre adquieren un aspecto similar al del bronce y las aleaciones que contienen mucho silicio (>12 %) pueden presentar un color desigual. La anodización dura, que tiene una coloración de tonos oscuros, permite un acabado con colores oscuros y opacos. Generalmente, se elige el color negro, tanto por su excelente aspecto estético como por su capacidad de uniformar el color en presencia de diferentes aleaciones.
Aleaciones de aluminio anodizables
Todas las aleaciones de aluminio son anodizables, con algunas pequeñas excepciones. Las mayores dificultades se encuentran en las aleaciones que contienen elementos distintos al aluminio en grandes cantidades, ya que es solo el aluminio el que contribuye a formar la capa de óxido. Como resultado, las aleaciones que contienen altas cantidades de cobre, como las de la serie 2000, no pueden alcanzar altos espesores y la capa de óxido será ligeramente menos compacta y menos resistente a la corrosión y al desgaste. Es posible que las aleaciones que contienen silicio en cantidades superiores al 12 % manifiesten un menor espesor y uniformidad del recubrimiento, con la consiguiente menor resistencia a la corrosión, al desgaste y, en ocasiones, falta de uniformidad de color.
Espesor de anodización
Una característica peculiar de la anodización es la posibilidad de recubrir las piezas con un espesor uniforme y calibrado en casi todas las superficies. Una excepción pueden ser los orificios de pequeño diámetro y muy profundos, para los cuales se debe evaluar individualmente la capacidad de penetración del recubrimiento.
El espesor estándar de la anodización dura es de 30-50 µm, aunque se pueden elegir espesores menores o mayores en función de necesidades específicas. En presencia de tolerancias muy estrechas se tiende a disminuir el espesor de anodización o a definir una tolerancia más estrecha, por ejemplo 30±5 µm.
Crecimiento dimensional
El espesor de tratamiento crece un 50 % en el exterior y un 50 % en el interior de la superficie de la pieza de aluminio. Por lo tanto, el aumento dimensional radial equivale a la mitad del espesor de tratamiento.
Resistencia a la corrosión
La anodización dura tiene una mayor resistencia a la corrosión que la anodización decorativa, gracias al mayor espesor y a la mayor compacidad de la capa de óxido. Esta resistencia puede verse afectada por las porosidades presentes en el recubrimiento, que son el primer punto de inicio de la corrosión. Para aumentar la resistencia a la corrosión, se realiza un tratamiento posterior a la anodización definido como fijación. Hay varios tipos de fijación y los dos más utilizados industrialmente y reconocidos internacionalmente son:
- Fijación en caliente: inmersión en agua a una temperatura de aproximadamente 95 °C, que permite una hidratación superficial de la capa de óxido de aluminio y cierra las porosidades, permitiendo una mejor resistencia a la corrosión.
- Fijación en frío: inmersión en una solución de fluoruro de níquel a temperatura ambiente. Las sales de níquel penetran en las porosidades del recubrimiento y mejoran la resistencia a la corrosión.
La fijación en caliente, a pesar de ser costosa en términos energéticos porque debe mantenerse a 95 °C, se utiliza cada vez más, en detrimento de la que se basa en sales de níquel, que son cancerígenas y pueden manifestar alergias en la piel. En el campo alimentario, por ejemplo, la fijación a base de níquel no se puede utilizar.
La anodización resiste óptimamente a la corrosión en contacto con alcoholes, hidrocarburos y soluciones neutras. Las soluciones ácidas o básicas disuelven el óxido de aluminio anulando el efecto barrera de protección contra la corrosión. La velocidad de disolución de la capa de anodización es proporcional a la acidez o basicidad de la solución, y es mayor en el caso de soluciones básicas.
La anodización dura OX-W es un tratamiento desarrollado específicamente para aumentar la ya excelente resistencia a la corrosión de la anodización dura. En algunas aleaciones permite alcanzar 1000 horas de exposición a niebla salina neutra según ISO 9227, sin aparición de corrosión. OX-W también es adecuado para proteger las aleaciones con alto contenido de silicio, en las que podrían presentarse dificultades con el proceso estándar de anodización.
Dureza, densidad y resistencia al desgaste
La anodización dura tiene una alta dureza, que varía en función de la aleación de aluminio utilizada.
La especificación ISO 10074 establece la dureza mínima que deben tener algunas aleaciones. La dureza se mide de acuerdo con la ISO 4516 en una capa con un espesor entre 25-50 µm y con una carga de 50 g HV 0,05.
Aleación | Dureza Vickers |
---|---|
Aleaciones de procesamiento de plástico | 400 HV |
Serie 2000 | 250 HV |
Serie 5000 con magnesio >2 % | 300 HV |
Serie 7000 | 300 HV |
Aleaciones de fusión con cobre <2 % y/o silicio <8 % | 250 HV |
La densidad, medida de acuerdo con la ISO 2106 en un recubrimiento de 50±5 µm sin fijación, debe tener los siguientes valores mínimos:
Aleación | Densidad del recubrimiento |
---|---|
Aleaciones de procesamiento de plástico | 1100 mg/dm² |
Serie 2000 | 950 mg/dm² |
Serie 5000 con magnesio >2 % | 950 mg/dm² |
Serie 7000 | 950 mg/dm² |
Aleaciones de fusión con cobre <2 % y/o silicio <8 % | 950 mg/dm² |
La elevada dureza y compacidad de la capa de óxido y la estructura columnar permiten que la anodización dura alcance una elevada resistencia al desgaste, mayor que el niquelado químico y comparable al cromado duro con espesor. El Taber Abraser es un test que determina el desgaste de los recubrimientos deslizantes en ruedas abrasivas. Según la ISO 10074, después de 10 000 ciclos, la pérdida de masa debe ser inferior a los siguientes valores:
Aleación | Pérdida máx. de peso |
---|---|
Aleaciones de procesamiento de plástico | 15 mg |
Serie 2000 | 35 mg |
Serie 5000 con magnesio >2 % | 25 mg |
Serie 7000 | 25 mg |
Aleaciones de fusión con cobre <2 % y/o silicio <8 % | - |
Rugosidad
La anodización dura contribuye a aumentar ligeramente la rugosidad superficial y se nota más en superficies con una baja rugosidad de procesamiento mecánico.
La anodización dura OX-W tiene la capacidad de limitar el aumento de la rugosidad superficial. Mediante el uso de algunas aleaciones de aluminio específicas y la definición de los parámetros operativos correctos, es posible mantener la rugosidad final en valores inferiores a 0,5 Ra.
Contacto con alimentos
La normativa «EN 14392 Requirements for anodized products for use in contact with foodstuff» especifica los requisitos de los tratamientos de anodización en piezas de aluminio destinadas al contacto con alimentos.
Los tratamientos realizados por Durox srl cumplen con la normativa EN 14392 si se respetan los siguientes requisitos:
- La composición química de las aleaciones de aluminio de las piezas a anodizar debe cumplir con los requisitos de las normativas EN 601 o EN 602, en la medida en que sean aplicables.
- Los tratamientos de anodización deben someterse a la fase de fijación que debe solicitarse expresamente.