Tras la caída del Muro de Berlín, a principios de los años 90, el mundo occidental empezó a investigar varias tecnologías rusas para evaluar su aplicabilidad en el plano industrial. Estas tecnologías provenían de la investigación rusa en el campo espacial y militar. Entre los tratamientos superficiales para los metales, adquirieron cierto interés los tratamientos electrolíticos denominados Plasma Electrolytic Oxidation PEO, también llamados Micro-Arc Oxidation MAO, que permitían crear una capa de óxido extremadamente dura y compacta sobre aluminio, magnesio y titanio, mediante el uso de corriente generada en presencia de alta tensión.
Micron Srl preparó la primera máquina CE derivada del modelo ruso en colaboración con Keronite e inició un programa de I+D para la mejora de las características de la capa de óxido creada utilizando corrientes diferentes y realizando variaciones en potencia y frecuencia. Los caminos de Micron y Keronite se separaron en un cierto punto y cada una continuó por su cuenta el programa de I+D.
El proceso de tratamiento PEO
El PEO se basa en el principio de aplicar una corriente en presencia de alta tensión, periódicamente invertida, a una pieza metálica anodizable que está sumergida en una solución especial definida como electrolito. Se consigue así crear una capa de óxido y al mismo tiempo fundir el metal gracias a las descargas debidas a la alta tensión que lo atraviesan. La pieza sumergida en el electrolito se cubre con innumerables pequeñas descargas eléctricas o «microarcos» que envuelven la pieza iluminándola mientras provocan la formación de la capa cerámica.
El resultado es la formación de una capa de óxido mineralizado por fusión, cuya dureza es igual a la del óxido original del metal. En el aluminio puro se alcanzan durezas similares a las de la alúmina Al2O3 de aproximadamente 2000 HV, en el titanio de alrededor de 1000 HV y en el magnesio en torno a 600 HV. En las aleaciones de aluminio de uso común, debido a los diferentes metales presentes en la aleación, se pueden alcanzar durezas comprendidas entre 1200 y 1600 HV.
Evolución del tratamiento PEO
La continua investigación y desarrollo ha llevado a una evolución y refinamiento del proceso de micro-spark o micro-arc, con una mejor distribución y refinamiento de las descargas del plasma electrolítico, lo que mejora las características superficiales y permite utilizar el recubrimiento cerámico sin reprocesamientos de lijado y con una mejor uniformidad de espesor.
Los electrolitos utilizados son soluciones ligeramente alcalinas, sin adición de metales pesados ni productos químicos peligrosos, lo que hace que el proceso sea ecológico y seguro para la salud de los trabajadores. Para cada uno de los tres metales, Al, Mg y Ti, se utilizan electrolitos y configuraciones de la máquina diferentes para la obtención de la capa cerámica superficial.
Micron ha desarrollado y evolucionado el tratamiento de Plasma Electrolytic Oxidation PEO sobre magnesio y aluminio, valiéndose también de la colaboración de una empresa inglesa. El uso de magnesio y sus aleaciones siempre ha estado limitado por su escasa resistencia a la corrosión, a pesar de su ligereza de 1,8 kg/dm³, su excelente procesabilidad y la posibilidad de ser moldeado a presión.
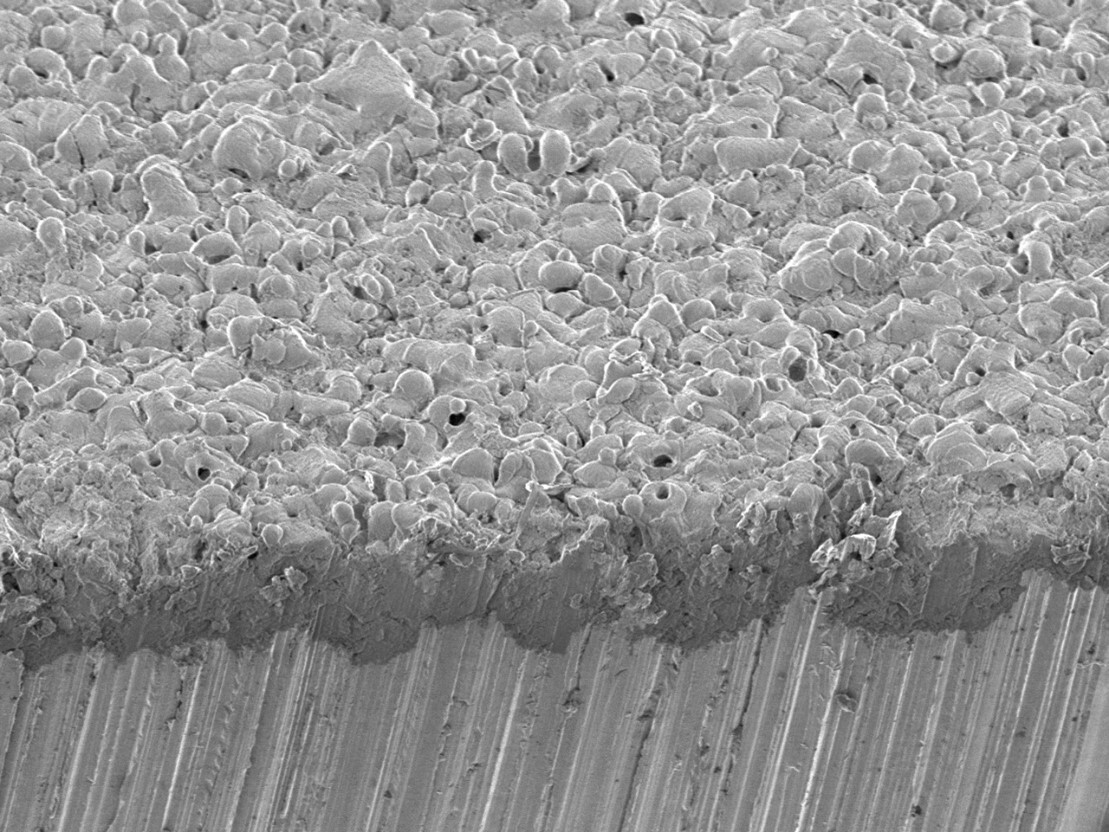
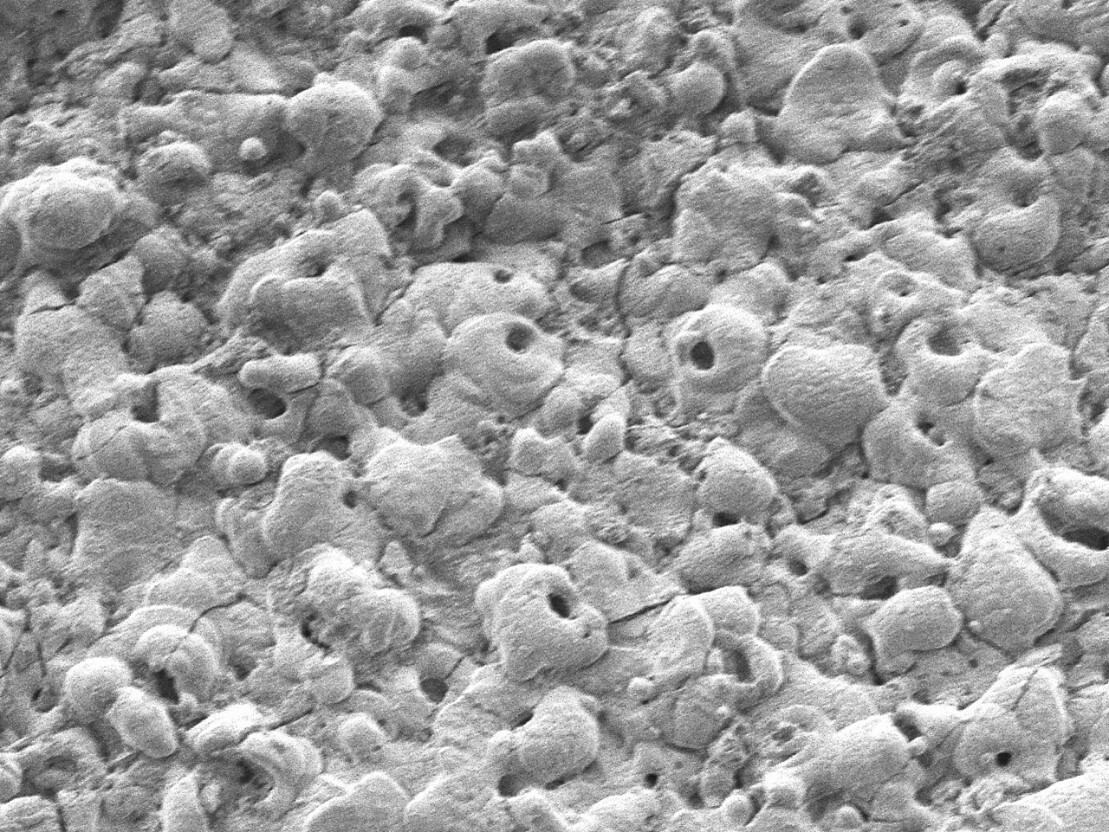
Características del recubrimiento PEO OX-UHA sobre magnesio
Antes de la llegada del PEO, para la protección contra la corrosión del magnesio se confiaba en los tratamientos HAE, en el anodizado clásico o en la cromación con Cr6, con resultados que no eran excelentes. Gracias al PEO, la capa cerámica —compuesta principalmente por óxidos mixtos de magnesio y aluminio— tiene una gran dureza (500 HV) y es compacta, a la vez que permite aumentar en gran medida la resistencia a la corrosión.
Una característica importante es también su estructura superficial, que proporciona una excelente adherencia a los tratamientos posteriores de impregnación o recubrimiento realizados con el fin de aumentar aún más la resistencia a la corrosión, logrando así alcanzar una resistencia a la corrosión sin igual.
Se pueden tratar con PEO OX-UHA todas las aleaciones de magnesio comunes, con espesores generalmente comprendidos entre 5 y 20 µm. El PEO permite tener una excelente resistencia a la corrosión a partir de espesores de recubrimiento bajos, gracias a su compacidad y adherencia. El PEO transforma la superficie de magnesio en óxido de magnesio, sin provocar ningún crecimiento dimensional debido al recubrimiento.
La dureza del recubrimiento varía en función de la aleación utilizada y generalmente se sitúa en valores comprendidos entre 400 y 600 HV, valores muy superiores a los de cualquier otro tratamiento de anodización del magnesio. La elevada dureza permite aumentar así la resistencia al desgaste, a los golpes y a los rasguños.
Tanto el proceso como el recubrimiento son respetuosos con el medio ambiente, ya que no hay productos químicos tóxicos ni cancerígenos. El PEO es el principal tratamiento alternativo a la cromatación, que debido a los problemas relacionados con el uso de cromo hexavalente se utiliza cada vez menos. El tratamiento PEO cumple con el reglamento REACH y la directiva RoHS, ya que no hay sustancias con restricciones de uso —más allá de las concentraciones máximas toleradas— y tampoco hay SVHC en cantidades superiores al 0,1 % en peso.