La anodización dura del aluminio es un proceso que permite crear en la superficie del material una capa de óxido de aluminio con propiedades de dureza y resistencia al desgaste superiores a las de la anodización natural o arquitectónica. Esto se debe a que la capa de anodización dura tiene un espesor mayor y se obtiene utilizando parámetros de proceso diferentes, como la temperatura del electrolito de anodización, que en la anodización dura es de aproximadamente 0 °C, frente a los 20 °C de la anodización arquitectónica. De esta manera, se obtiene un recubrimiento duro y resistente al desgaste, adecuado para diferentes tipos de aplicaciones.
La dureza
Como se mencionó anteriormente, la anodización dura presenta una dureza elevada, que depende de la aleación de aluminio utilizada. En general, la dureza de los tratamientos de anodización dura varía de 280 a 500 HV, dependiendo de la aleación elegida. Por ejemplo, las aleaciones de aluminio de la serie 6000 son particularmente adecuadas para obtener capas de anodización dura de elevada dureza, mientras que las aleaciones de la serie 2000 —debido a su contenido de cobre— alcanzan valores de dureza más bajos, aproximadamente 280 HV. Las aleaciones de la serie 7000 se sitúan entre medias y pueden alcanzar una dureza de aproximadamente 350 HV.
La resistencia al desgaste
La resistencia al desgaste de los recubrimientos de anodización dura es una propiedad estrechamente relacionada con la dureza del tratamiento. Cuanto mayor sea la dureza, mayor será la resistencia al desgaste. Para medir la resistencia al desgaste de los recubrimientos de anodización dura, se utiliza comúnmente la prueba de resistencia a la abrasión Taber Abraser, que consiste en realizar una prueba de abrasión en una muestra frotándola con ruedas abrasivas. La resistencia a la abrasión se calcula en función de la pérdida de peso de la muestra antes y después de la prueba, que consta de 10 000 ciclos de abrasión.
Según los resultados obtenidos con el test Taber Abraser, las aleaciones de aluminio de la serie 6000 presentan la mayor resistencia a la abrasión, seguidas de las aleaciones de la serie 7000. Por contra, las aleaciones de la serie 2000 presentan la menor resistencia al desgaste. No obstante, es importante destacar que la resistencia al desgaste de los recubrimientos de anodización dura es generalmente muy elevada, superior a la de las aleaciones de acero y al niquelado químico, y comparable a la del cromo duro.
Aplicaciones para la resistencia al desgaste
Además de conferir una elevada resistencia a la corrosión, los tratamientos de anodización dura se utilizan para aumentar la resistencia al desgaste de las aleaciones de aluminio.
En el sector de la automoción, por ejemplo, la anodización dura se aplica a menudo sobre componentes mecánicos como cuerpos de válvula, vástagos y elementos flotantes, que pueden estar sometidos a roces y abrasiones durante su uso. Gracias a la dureza y resistencia al desgaste de la superficie anodizada, estos componentes tienen una vida útil más larga. En el sector de las bicicletas, la anodización dura se utiliza, por ejemplo, en coronas para resistir la abrasión causada por el paso de la cadena. Además, en el sector de las máquinas industriales, la anodización dura se aplica a menudo a rodillos de transferencia de máquinas de impresión o envasadoras para reducir el desgaste causado por el roce con papel u otros materiales. También en el sector textil, varias partes se tratan con anodización dura para resistir el desgaste debido a las rozaduras con otras partes o con la fibra textil.
Conclusiones
En resumen, la anodización dura es un tratamiento superficial que permite conferir a las aleaciones de aluminio propiedades de dureza y resistencia al desgaste superiores a las de la anodización natural o arquitectónica. La dureza de los recubrimientos de anodización dura varía en función de la aleación de aluminio utilizada, pero en general está entre 280 y 500 HV. La resistencia al desgaste se mide con el test de resistencia a la abrasión Taber Abraser y también depende de la aleación elegida. En general, las aleaciones de las series 6000 y 7000 presentan la mayor resistencia a la abrasión, mientras que las aleaciones de la serie 2000 presentan la menor resistencia al desgaste. No obstante, es importante destacar que la resistencia al desgaste de los recubrimientos de anodización dura es generalmente muy elevada, superior a la de las aleaciones de acero y al niquelado químico.
La anodización dura se utiliza en diferentes sectores industriales, como la automoción, el sector de las bicicletas, el sector de las máquinas industriales y el sector textil, para aumentar la duración y la resistencia al desgaste de componentes sujetos a roces y abrasiones. De esta manera, la anodización dura representa una solución eficaz para mejorar el rendimiento y la vida útil de muchos productos.
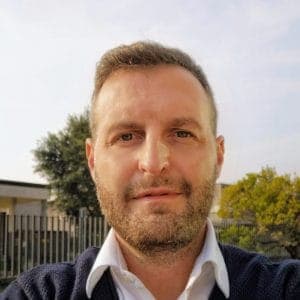