Una de las propiedades principales del tratamiento de niquelado químico es su resistencia a la corrosión. De hecho, el niquelado químico se utiliza en partes mecánicas metálicas (aceros, aleaciones de aluminio o cobre) en caso de necesidad de protección contra la oxidación y la corrosión debidas a agentes externos.
Se utiliza, por ejemplo, para proteger partes de maquinaria industrial (máquinas de embalaje, máquinas herramienta, máquinas textiles), dispositivos mecánicos varios (válvulas neumáticas, actuadores, racores) y en el sector de la automoción (pistones de freno, componentes internos, engranajes).
El niquelado químico permite aumentar la resistencia a la corrosión gracias a la resistencia química de la capa de níquel depositada. La capa está compuesta por una aleación binaria de níquel y fósforo Ni-P con concentraciones de fósforo del 5 al 13 %. Esta aleación presenta una elevada resistencia a la agresión química. No es atacada por soluciones salinas neutras y resiste bien los ambientes alcalinos o ligeramente ácidos. La capa de níquel químico no es atacada por agentes químicos que se encuentran generalmente en atmósferas de ambientes cerrados o abiertos, civiles, industriales o viales.
La capa de níquel químico protege contra la corrosión porque actúa como barrera y aísla el material base de los agentes agresivos externos, impidiendo, retrasando o limitando los puntos de ataque corrosivos. Cada punto de discontinuidad de la capa (defectos, porosidad, inclusiones, grietas) puede causar un inicio de la corrosión.
El espesor influye de manera importante en la presencia o no de estas discontinuidades. Cuanto mayor sea el espesor, menor será la «porosidad» de la capa y, por lo tanto, menores serán los puntos de posible inicio de la corrosión.
La influencia del material base en la elección del espesor de niquelado químico
La elección del espesor de niquelado químico correcto en base a las necesidades de resistencia a la corrosión depende del material base que se desea proteger. El comportamiento frente a la corrosión varía en función del material base, ya que entran en juego factores electroquímicos entre la base y el recubrimiento.
Además del material base y el espesor, existen muchos otros factores que influyen en la resistencia a la corrosión de las piezas niqueladas. Puede encontrar más información en el artículo Los factores que influyen en la resistencia a la corrosión del niquelado químico .
Espesor de niquelado en aleaciones de hierro
En el caso de que el material base sea una aleación de hierro, la ausencia de porosidad de la capa es muy importante. En los aceros, cada punto de discontinuidad de la capa puede causar un inicio de corrosión del material base en un ambiente agresivo. Además, debido a la diferencia de potencial de reducción entre el níquel y el material base, en estos materiales se puede generar un fenómeno de corrosión galvánica.
Por lo tanto, en caso de las aplicaciones en las que la pieza niquelada puede entrar en contacto con agua, humedad o sustancias agresivas, es necesario prever espesores mayores en función de la agresividad del ambiente. En la siguiente tabla se muestran los valores de espesor recomendados.
Espesor de niquelado en aleaciones de aluminio
Se puede hacer un razonamiento similar a las aleaciones de hierro para las aleaciones de aluminio con una pequeña aclaración. La resistencia a la corrosión del niquelado químico en aluminio es más crítica, ya que puede sufrir un fenómeno de corrosión subyacente.
Para evitar este problema hemos optimizado nuestro proceso de preparación y activación de las aleaciones de aluminio. Esto nos permite garantizar la máxima resistencia a la corrosión, hasta el punto que aplicamos el niquelado químico en piezas de aluminio de seguridad en el sector de la automoción (pistones de freno) en las que se requiere una resistencia a la corrosión de 720 horas en niebla salina (<5 % de área corroída).
Se ha desarrollado un tratamiento de niquelado químico específico para maximizar la resistencia a la corrosión de las aleaciones de aluminio, el tratamiento Niplate eXtreme .
Espesor de niquelado en aleaciones de cobre
En el caso de material base de aleación de cobre, en cambio, la presencia de porosidad tiene muy poca influencia en el comportamiento a la corrosión de la pieza recubierta. Esto se debe a que el material base y la capa tienen un potencial de reducción muy similar y, por lo tanto, no se crea un par galvánico. Además, las aleaciones de cobre tienen una mayor resistencia a la corrosión y, por lo tanto, en caso de inicio de la corrosión, el efecto es más limitado.
Las piezas de aleación de cobre con tratamiento de niquelado químico se pueden utilizar en el ambiente marino incluso en inmersión con espesores de niquelado limitados (15-20 µm).
Espesores de niquelado recomendados
La elección del espesor no siempre es simple y directa, también porque las aplicaciones de las piezas niqueladas son muy variadas. A veces es solo la prueba práctica en el entorno de aplicación real la que permite definir el espesor correcto.
En la siguiente tabla se muestran valores indicativos de espesor de niquelado químico en función de la condición de funcionamiento.
Condición de funcionamiento | Descripción | Espesor de recubrimiento en aleaciones de hierro y aluminio | Espesor de recubrimiento en aleaciones de cobre |
---|---|---|---|
1 – Ligero | Uso en ambiente interior en atmósfera cálida y seca | 8±2 µm | 5±2 µm |
2 – Moderado | Ambiente interior donde puede producirse condensación. Ambientes interiores industriales en condiciones secas. | 15±2 µm | 8±2 µm |
3 – Exigente | Uso al aire libre con humectación frecuente por lluvia, humedad o agua. | 30±3 µm | 15±2 µm |
4 – Extremadamente exigente | Uso al aire libre en ambiente marítimo y en condiciones ambientales agresivas con humectación frecuente por lluvia, humedad o agua que contiene sales de pH neutro o ligeramente alcalino. | 50±5 µm | 20±2 µm |
Para más información o consejos sobre el espesor de tratamiento correcto a aplicar, no dude en ponerse en contacto con nosotros.
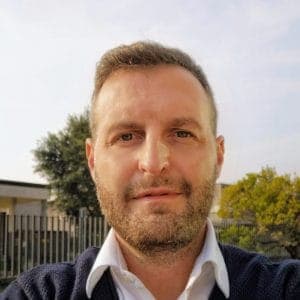