Diferencia entre niquelado químico y recubrimientos galvánicos
Los recubrimientos galvánicos (por ejemplo, cromado, niquelado electrolítico, galvanizado o zinc-níquel) se depositan mediante el uso de corriente continua aplicada a la pieza, lo que permite la deposición del metal en la superficie de la pieza por recubrir.
La corriente aplicada tiende a descargarse siguiendo el camino de menor resistencia y, en consecuencia, el espesor del recubrimiento galvánico es mayor en las superficies externas de las piezas y en las esquinas, y es menor (o incluso ni existe) en las cavidades internas cuando la pieza recubierta es bastante compleja.
En cambio, el niquelado químico es un proceso de deposición de una aleación de níquel y fósforo que se produce a través de una reacción química de óxido-reducción, sin el uso de corriente. Su característica principal es que recubre todas las superficies de la pieza con un espesor uniforme y calibrado.
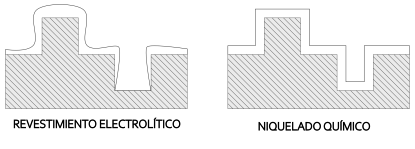
Modo de protección contra la corrosión Hay dos tipos de comportamiento del recubrimiento que afectan a la resistencia a la corrosión de la pieza recubierta:
- Efecto sacrificial
- Efecto barrera
EFECTO SACRIFICIAL
Es la típica protección contra la corrosión de los recubrimientos a base de zinc y zinc níquel. El zinc tiene un valor de potencial electroquímico menor que el hierro y, por lo tanto, se convierte en sacrificial al corroerse primero, por lo que evita la corrosión del hierro. Solo cuando el zinc se haya disuelto casi por completo, dejando zonas descubiertas, comenzará la corrosión del hierro, que progresará rápidamente. Un ejemplo típico de corrosión sacrificial es el ánodo de magnesio insertado en los calentadores domésticos que previene la corrosión del acero, ya que el magnesio es sacrificial. Otro ejemplo son los ánodos de zinc o magnesio utilizados en los cascos de las embarcaciones. Por esta razón, para evaluar la resistencia a la corrosión de las piezas galvanizadas, se considera el tiempo transcurrido antes de la aparición de productos de corrosión blancos (óxido de zinc) y la aparición de productos de corrosión rojos (óxido de hierro). Un ejemplo de requisito típico (para el galvanizado) de resistencia a la corrosión después de la exposición a niebla salina neutra según la ISO 9227 es 96 horas sin aparición de corrosión blanca y 168 horas sin aparición de corrosión roja.
EFECTO BARRERA
La aleación de níquel fósforo depositada mediante el proceso de niquelado químico tiene un potencial electroquímico mayor que el hierro y el aluminio y, por lo tanto, no es sacrificial en comparación con ellos. Actúa como protección contra la corrosión, ya que crea una capa barrera que ejerce una acción impermeabilizante contra los agentes agresivos externos. La aleación de níquel fósforo tiene una elevada resistencia química y casi no se corroe con soluciones salinas neutras, especialmente el Niplate 500 con alto contenido en fósforo. Por este motivo, considerando solo el recubrimiento, se pueden alcanzar miles de horas de exposición a niebla salina sin corrosión. Sin embargo, se debe tener en cuenta que cualquier posible imperfección del recubrimiento puede generar corrosión del material subyacente, incluso después de unas pocas horas de exposición a la niebla salina. Las causas de estas imperfecciones pueden ser múltiples y entre las principales encontramos:
- Porosidad del recubrimiento debido al propio proceso de niquelado o a inclusiones/defectos en el material base.
- Superficies dejadas en bruto y, por lo tanto, caracterizadas por defectos de trefilado e inclusiones superficiales.
- Grasas, aceites y pastas de difícil eliminación.
- Aristas vivas y rebabas.
Por lo tanto, para el niquelado químico no tiene sentido asignar un límite para la aparición de óxido rojo, que puede aparecer incluso después de unas pocas horas de exposición cuando el recubrimiento tiene un pequeño defecto. La gran ventaja del niquelado químico es la capacidad de mantener el sustrato protegido incluso después de muchas horas de exposición a la niebla salina, manifestando solo una leve corrosión por picadura inicial y, en consecuencia, un área de superficie corroída muy baja.
Por lo tanto, generalmente se asigna una calificación de protección después de la exposición a la niebla salina para un número de horas decidido por el diseñador, como se detalla a continuación.
Evaluación de la resistencia a la corrosión del niquelado químico La resistencia a la corrosión de los productos recubiertos con niquelado químico se evalúa habitualmente mediante pruebas de niebla salina neutra (NSS) de acuerdo con las siguientes dos especificaciones:
Norma | Descripción |
---|---|
ISO 9227 | Pruebas de corrosión en atmósferas artificiales - Pruebas en niebla salina |
ASTM B117 | Standard Practice for Operating Salt Spray (Fog) Apparatus |
Después del test de niebla salina, la evaluación de la resistencia a la corrosión se realiza mediante la especificación UNI EN ISO 10289: Evaluación de muestras y productos sometidos a pruebas de corrosión. Esta última asigna una calificación de protección en función del área corroída con respecto al área expuesta a niebla salina, como se resume en la siguiente tabla:
Área de los defectos A (%) | Clasificación |
---|---|
Ningún defecto | 10 |
0 < A ≤ 0,1 | 9 |
0,1 < A ≤ 0,25 | 8 |
0,25 < A ≤ 0,5 | 7 |
0,5 < A ≤ 1 | 6 |
1 < A ≤ 2,5 | 5 |
2,5 < A ≤ 5 | 4 |
5 < A ≤ 10 | 3 |
10 < A ≤ 25 | 2 |
25 < A ≤ 50 | 1 |
50 < A | 0 |
Un ejemplo de calificación es el siguiente: Clasificación 7 después de 500 horas de exposición a niebla salina neutra ISO 9227.
Normalmente, el niquelado químico resiste bien a la corrosión cuando se elige el espesor adecuado en función de la agresividad del entorno en el que se utiliza el componente y cuando las superficies tienen un buen acabado de procesamiento mecánico. Van desde espesores de 5-10 µm para ambientes no particularmente expuestos, 20 µm para corrosiones moderadas, hasta 50 µm para ambientes agresivos como el entorno marino.
La mejor resistencia a la corrosión en aleaciones de hierro y cobre la proporciona el níquel químico de alto contenido en fósforo Niplate ®500 gracias a su estructura amorfa con baja porosidad, incluso con espesores de pocas micras. El níquel químico crea la mejor protección contra la corrosión hacia el metal base cuando se trata de aleaciones de cobre, en particular con el latón, que se utiliza ampliamente para piezas mecánicas. La diferencia de electronegatividad entre las aleaciones de Cu-Zn y de Ni-P es casi nula, lo que contribuye a evitar la agresión de la pieza de latón niquelado químicamente. La resistencia a la corrosión supera en este caso las 1000 horas en niebla salina neutra NSS según ISO 9227.
Para el aluminio, el tratamiento utilizado principalmente para conferir resistencia a la corrosión es la anodización. Si además de esta característica se busca tener una superficie deslizante con baja rugosidad, resistente al desgaste y conductiva, el mejor recubrimiento es el Niplate eXtreme. Se trata de un recubrimiento de níquel químico diseñado específicamente para mejorar la resistencia a la corrosión de las aleaciones de aluminio. Para aleaciones con alto contenido de silicio, como las aleaciones de fundición a presión, le recomendamos que se ponga en contacto con nosotros para proponerle la mejor solución en función de la aleación y de su composición.