La energía limpia se ha convertido en una prioridad absoluta para los gobiernos e industrias de todo el mundo, ya que la reducción de las emisiones de gases de efecto invernadero se ha vuelto algo fundamental para limitar el impacto del cambio climático. En este contexto, el hidrógeno está emergiendo como una fuente de energía limpia prometedora para los vehículos y otras aplicaciones.
Los vehículos de hidrógeno ofrecen ventajas significativas sobre los vehículos eléctricos, especialmente para aplicaciones que requieren el transporte de cargas pesadas a largas distancias. Gracias a su mayor autonomía y capacidad de reabastecimiento rápida, estos vehículos son especialmente adecuados para el transporte de mercancías por carretera a largas distancias, donde las limitaciones de la autonomía de las baterías y los largos tiempos de carga son obstáculos significativos.
Esta característica, combinada con la posibilidad de producir hidrógeno con energías renovables a nivel local, hace que los vehículos de hidrógeno sean una opción ecológica, particularmente efectiva para reducir las emisiones de gases de efecto invernadero en comparación con los vehículos de combustibles fósiles, lo que contribuye significativamente a la reducción del impacto ambiental en el sector del transporte.
En resumen, el hidrógeno está emergiendo como una fuente de energía limpia prometedora para los vehículos. Con la infraestructura de apoyo adecuada, el hidrógeno podría ser una solución importante para garantizar la transición ecológica en los sectores del automóvil, los vehículos pesados y los industriales.
La necesidad de proteger las piezas mecánicas contra la corrosión y el desgaste
La protección de los componentes del circuito de hidrógeno es de fundamental importancia para garantizar la seguridad y la fiabilidad de los vehículos de hidrógeno. Los componentes mecánicos del circuito de hidrógeno deben resistir la corrosión y el desgaste derivados de la agresión de las sustancias químicas presentes en la carretera, como el agua, las sales, los hidrocarburos y otros contaminantes ambientales.
Es importante destacar que las altas presiones de hidrógeno también pueden causar problemas de fugas si las superficies de sellado de los componentes del circuito de hidrógeno se corroen con el tiempo. El hidrógeno es altamente inflamable y cualquier fuga podría crear un ambiente explosivo. Por esta razón, la seguridad de los vehículos con propulsión de hidrógeno también depende de la capacidad de los componentes del circuito de hidrógeno para resistir la corrosión y el desgaste durante la vida útil del vehículo.
La solución: el niquelado químico y la anodización del aluminio como tratamientos superficiales protectores
El uso de tratamientos superficiales puede aumentar la resistencia de los componentes a las tensiones mecánicas y a la corrosión de los componentes del circuito de hidrógeno, al prolongar su vida útil y garantizar un funcionamiento fiable y seguro de los vehículos de hidrógeno.
El niquelado químico y la anodización son dos tratamientos superficiales que se pueden utilizar para proteger los componentes del circuito de hidrógeno contra la corrosión y el desgaste.
El niquelado químico es un proceso de deposición química de una capa de aleación de níquel y fósforo en la superficie del material que se pretende proteger. Esta capa de níquel ofrece protección contra la corrosión y el desgaste, al resistir la corrosión tanto en ambientes ácidos como alcalinos. Además, el niquelado químico se puede utilizar para proteger contra la corrosión todas las aleaciones metálicas principales, incluidas las aleaciones de hierro, cobre y aluminio.
La anodización, por otro lado, es un proceso electroquímico que se utiliza para proteger las aleaciones de aluminio contra la corrosión y el desgaste. Durante la anodización, se crea una capa de óxido de aluminio en la superficie del aluminio. Esta capa de óxido de aluminio actúa como una barrera protectora contra la corrosión y el desgaste y se puede colorear con fines estéticos.
En resumen, el niquelado químico y la anodización son soluciones eficaces para proteger los componentes del circuito de hidrógeno contra la corrosión y el desgaste. Estos tratamientos superficiales ofrecen una elevada protección contra la agresión química, así como una mayor resistencia mecánica contra los esfuerzos derivados de las altas presiones a las que se somete el hidrógeno.
En la siguiente tabla se resumen las características principales de estos recubrimientos y el grado de protección indicativo que pueden ofrecer.
Características | Niquelado químico | Anodización |
---|---|---|
Metales que se pueden recubrir | Aleaciones de aluminio Aleaciones de cobre Aleaciones de hierro | Aleaciones de aluminio |
Resistencia a la corrosión en ambientes con pH neutro | ★★★★☆ en aleaciones de aluminio ★★★★★ en aleaciones de cobre ★★★★☆ en aleaciones de hierro | ★★★★★ en aleaciones de aluminio |
Resistencia a la corrosión en ambientes con pH ligeramente ácido | ★★★☆☆ en aleaciones de aluminio ★★★★☆ en aleaciones de cobre ★★★☆☆ en aleaciones de hierro | ★★☆☆☆ en aleaciones de aluminio |
Resistencia a la corrosión en ambientes con pH ligeramente alcalino | ★★★☆☆ en aleaciones de aluminio ★★★★★ en aleaciones de cobre ★★★★☆ en aleaciones de hierro | ★★☆☆☆ en aleaciones de aluminio |
Resistencia al desgaste | ★★★☆☆ en aleaciones de aluminio ★★★★☆ en aleaciones de cobre ★★★★☆ en aleaciones de hierro | ★★★★★ en aleaciones de aluminio |
Los componentes del circuito de hidrógeno que pueden beneficiarse del niquelado químico y la anodización
Placas bipolares de los «stacks» de los electrolizadores para producción de H2
Las placas bipolares son componentes esenciales de los electrolizadores, ya que en su superficie se produce la reacción de oxidación-reducción inducida por la corriente continua que transforma el agua en H₂ y O₂ gaseosos. Estas superficies deben ser conductoras y deben resistir la corrosión de las soluciones acuosas alcalinas o ácidas necesarias para la producción de gas H2 y O2.
En estos componentes, el niquelado químico puede ofrecer soluciones técnicamente ventajosas y económicamente viables para la protección contra la corrosión y el mantenimiento de la conductividad para algunos tipos de electrolizadores (PEM, AEM, AEMWE) donde las placas bipolares son de acero al carbono, acero inoxidable o titanio.
La alternativa al niquelado químico está dada por recubrimientos de metales preciosos como oro, platino, iridio o por recubrimientos en fase gaseosa como los PVD o CVD que tienen costes mucho más altos y son poco viables a gran escala. Es muy importante que para el sector de los electrolizadores —que tendrá dimensiones globales enormes en el máximo de su evolución— se puedan utilizar tecnologías y materiales de alta disponibilidad y con costes reducidos.
El niquelado químico tiene una excelente resistencia a la corrosión y puede proteger las placas bipolares frente a las reacciones de disolución y oxidación que se producen en el cátodo y en el ánodo del «stack» o celda electrolítica.
Nuestra competencia en la aplicación del niquelado químico en placas bipolares, combinada con nuestra capacidad para tratar grandes volúmenes con eficiencia, sitúa a Micron srl a la vanguardia como socio para la producción a escala de electrolizadores de hidrógeno, especialmente ahora que la demanda se está acelerando.
Micron ha desarrollado y produce internamente las formulaciones para el niquelado químico y ha perfeccionado la experiencia técnica necesaria para garantizar un niquelado químico eficaz en diferentes tipos de acero inoxidable y titanio.
Para más información sobre nuestros servicios de niquelado químico y para saber cómo podemos apoyar su proyecto de electrolizadores para la producción de hidrógeno, no dude en ponerse en contacto con nosotros. Visite nuestro sitio web o póngase en contacto con nosotros directamente para cualquier consulta que tenga o para solicitar un presupuesto.
Componentes mecánicos del sistema de almacenamiento y transferencia del H2 en los vehículos
Los componentes del circuito de hidrógeno de los vehículos eléctricos —incluidos los cuerpos de válvula, los reductores y las partes de los cilindros— a menudo necesitan protección contra la corrosión. El niquelado químico y la anodización pueden proteger estos componentes contra la corrosión y el desgaste, prolongando su vida útil y resistencia.
Los cilindros, los cuerpos de válvula y los reductores, utilizados para el almacenamiento, el control del flujo y la regulación de la presión del hidrógeno, pueden estar sometidos a corrosión y desgaste debido a la fricción mecánica y a la exposición a los agentes atmosféricos y otros agentes agresivos. El niquelado químico y la anodización pueden proteger los cuerpos de válvula contra la corrosión y el desgaste, aumentando su resistencia y prolongando su vida útil.
A menudo estos componentes se construyen en aleaciones de aluminio, un material económico, fácilmente procesable y ligero. Durox tiene una amplia experiencia sobre el mejor modo de aplicación de la oxidación anódica del aluminio para un resultado que cumple con los requisitos más estrictos de calidad y fiabilidad para estos componentes.
Conclusiones: la importancia de la protección superficial
En conclusión, la protección de los componentes del circuito de hidrógeno mediante el niquelado químico o la anodización es una oportunidad para garantizar la seguridad y la vida útil de los vehículos de hidrógeno. La corrosión y el desgaste de los componentes mecánicos pueden causar pérdidas de hidrógeno y potencialmente crear situaciones peligrosas. El niquelado químico y la anodización pueden mejorar la vida útil, garantizando una mayor seguridad de la cadena de producción y uso del hidrógeno como fuente de energía limpia.
El hidrógeno representa una solución importante para la transición hacia un futuro sostenible y la protección de los componentes relacionados con su producción y uso es un aspecto fundamental para garantizar la seguridad y la eficacia de los vehículos de hidrógeno en este escenario.
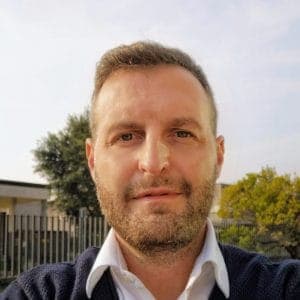