Los recubrimientos de niquelado químico a menudo se aplican a las piezas mecánicas por su capacidad de potenciar una importante propiedad: la resistencia a la corrosión.
La capa de níquel químico, de hecho, presenta una elevada resistencia química y una uniformidad de espesor. Estas características permiten crear una barrera entre la aleación base y el entorno exterior, lo que aumenta significativamente la resistencia a la corrosión de la pieza.
Este mecanismo de protección contra la corrosión es completamente diferente al que ofrecen otros recubrimientos como el galvanizado sobre hierro. De hecho, en el caso del galvanizado, la capa de zinc presente en la superficie es sacrificial respecto al metal base. La capa de zinc no tiene una resistencia química, pero se corroe antes que el acero de la base. Es precisamente esta característica de ser sacrificial respecto al hierro la que permite proteger la base contra la corrosión.
El recubrimiento de níquel químico protege contra la corrosión creando una barrera hacia el entorno exterior. Los puntos de posible inicio de la corrosión son aquellas zonas en las que el recubrimiento no es continuo.
La continuidad e integridad del recubrimiento, es decir, el grado de protección contra la corrosión, dependen de aquellos factores que pueden comprometer la continuidad de la capa. Los factores que más influyen en el resultado son principalmente atribuibles a los procesos realizados antes del niquelado químico.
Los principales factores son los siguientes:
- Recubrimiento
- Tipo de níquel químico (de medio/alto contenido en fósforo)
- Espesor de recubrimiento
- Pieza por recubrir
- Aleación metálica de la pieza
- Tecnología de producción (fundición, moldeo, procesamiento mecánico…)
- Geometría de la pieza (presencia de aristas, roscas…)
- Acabado superficial y rugosidad (superficies torneadas, fresadas, rectificadas, en bruto, granalladas…)
Recubrimiento
Tipo de níquel químico
El tipo de niquelado químico —con níquel químico de contenido medio o alto en fósforo— influye en la resistencia a la corrosión. De hecho, el niquelado químico de alto contenido en fósforo presenta —a igualdad de espesor— una mayor uniformidad y continuidad de la capa.
Por lo tanto, las piezas recubiertas con níquel químico de alto contenido en fósforo Niplate 500 tendrán, en general, un mejor comportamiento frente a la corrosión que las piezas con níquel químico de medio contenido en fósforo Niplate 600.
Espesor de recubrimiento
El espesor de recubrimiento también influye en la resistencia a la corrosión. Cuanto mayor sea el espesor de recubrimiento, mayor será la cobertura, continuidad y uniformidad del recubrimiento.
El espesor elegido depende en gran medida de la aplicación, del tipo de níquel químico y del material base de la pieza. En general, cuando se requiere una elevada resistencia a la corrosión, el espesor de recubrimiento debe ser superior a 20 µm en el caso de piezas de aleación de hierro o aluminio. Para piezas de aleación de cobre es suficiente un espesor de 10 µm.
Pieza por recubrir
Aleación metálica de la pieza
El comportamiento frente a la corrosión depende en gran medida de la aleación metálica recubierta. Esto se debe a que en la interfaz entre el metal base y el recubrimiento se crea un par galvánico entre los dos metales que puede crear fenómenos de aceleración de la corrosión:
- Las aleaciones de cobre recubiertas con níquel químico presentan la mejor resistencia a la corrosión. Estas aleaciones tienen un potencial de reducción similar al del recubrimiento y, por lo tanto, no se crea un par galvánico en la interfaz. Las aleaciones de cobre recubiertas pueden superar fácilmente las 720 horas de niebla salina sin corrosión, incluso con espesores de recubrimiento bajos (aproximadamente 10 µm).
- Por otro lado, las aleaciones de hierro y las de aluminiopresentan un potencial de reducción menor que el recubrimiento. Esto crea un par galvánico que acelera la corrosión en la interfaz. En este caso, para tener una buena resistencia a la corrosión, es necesario aumentar el espesor de tratamiento (generalmente por encima de 20 µm). El aumento de espesor permite mejorar la continuidad de la capa y, por lo tanto, evitar que haya inicios de corrosión, eliminando así el problema del par galvánico entre la base y el recubrimiento.
Tecnología de producción
Las mejores prestaciones en términos de resistencia a la corrosión se obtienen para piezas producidas mediante procesamiento mecánico. Esto se debe a que el procesamiento mecánico, a diferencia de la fundición, garantiza una superficie con un mejor acabado, menor rugosidad y ausencia de porosidad.
Las piezas obtenidas por fundición, ya sea aluminio o hierro fundido, presentan en la superficie porosidad, inclusiones u otros defectos que comprometen la continuidad de la capa y, por lo tanto, permiten el inicio de la corrosión.
Geometría de la pieza
La geometría de la pieza también puede influir en la resistencia a la corrosión. De hecho, la presencia de aristas afiladas o roscas puede influir en esas zonas en la continuidad del recubrimiento y, por lo tanto, crear zonas de inicio de la corrosión. Por lo tanto, para mejorar las prestaciones en términos de resistencia a la corrosión, es una buena práctica suavizar los bordes de la pieza siempre que sea posible.
Acabado superficial y rugosidad
El tipo de procesamiento mecánico y la rugosidad de la superficie influyen significativamente en la resistencia a la corrosión (especialmente en aleaciones de hierro y aluminio).
De hecho, donde la rugosidad superficial es alta (>1,00 Ra) o el material presenta desgarros, rebabas o imperfecciones, es fácil que se presenten inicios de corrosión. Esto se debe al hecho de que en esas zonas el recubrimiento no puede cubrir la superficie de forma continua.
Conclusiones
Los factores que influyen en la resistencia a la corrosión son muchos y es difícil sintetizarlos porque están relacionados entre sí. La elección de las especificaciones de tratamiento también depende en gran medida de la aplicación en que se vaya a usar la pieza.
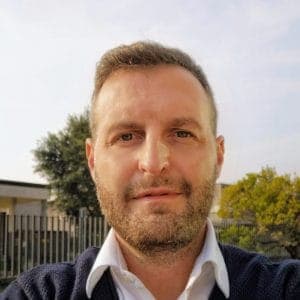