En la mecánica de precisión, las principales aleaciones metálicas utilizadas son las aleaciones de hierro, aluminio y cobre, gracias a sus características mecánicas y su disponibilidad, así como por su bajo coste y fácil mecanización.
La evolución del mercado y de las tecnologías ha supuesto inevitablemente la búsqueda y la demanda de características cada vez mejores, también en lo que respecta a las características superficiales. Las tres aleaciones mencionadas a menudo presentan características superficiales insuficientes, como, por ejemplo, la resistencia a la corrosión o la resistencia al desgaste. Por lo tanto, muy a menudo es necesario aumentar algunas características superficiales mediante la aplicación de recubrimientos que puedan satisfacer diversos requisitos técnicos o estéticos.
El niquelado químico es el recubrimiento que más se presta a ser aplicado a piezas mecánicas de precisión, ya que combina múltiples características, como, por ejemplo, la uniformidad de espesor, una alta dureza, resistencia al desgaste y excelente resistencia a la corrosión.
El proceso de niquelado químico se realiza por inmersión en una solución de níquel mediante un proceso químico de reacción autocatalítica, sin el uso de corriente. Sobre la superficie de la pieza a tratar se deposita una aleación de níquel fósforo por medio de la reacción de oxidación-reducción entre el catión Ni++ dado por el sulfato de níquel y el anión H2PO2 originado por el hipofosfito sódico (agente reductor).
Este proceso permite tener un recubrimiento con espesores uniformes y calibrados en todas las superficies —incluso las internas— y con geometrías complejas. Esto permite también respetar tolerancias estrechas sin tener que prever aislamientos o reelaboraciones de superficies sujetas a tolerancias. El recubrimiento completo de la pieza también permite proteger contra la corrosión y el desgaste todas las superficies internas, como cilindros, canales, racores y distribuidores de aire, agua, vapor o gases para aplicaciones médicas.
En los procesos galvánicos (también llamados electrolíticos), como el cromado o el niquelado electrolítico, se utiliza la corriente eléctrica para la deposición del recubrimiento metálico, lo que inevitablemente conduce a mayores espesores en las esquinas y dificultades para recubrir las zonas internas.
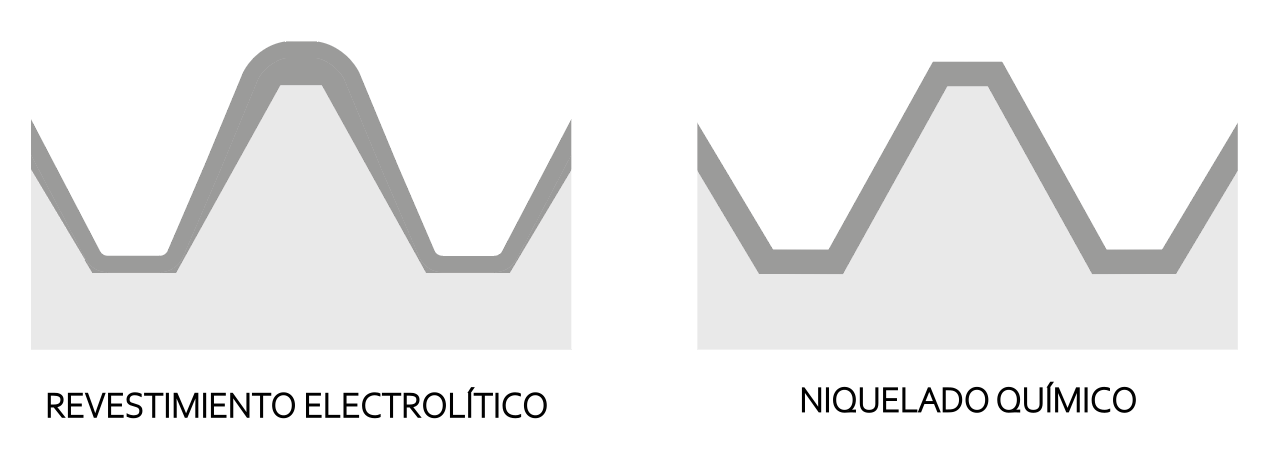
Niquelado químico y niquelado electrolítico
Se pueden decir que el niquelado químico y electrolítico solo tienen en común el tipo de metal. Los procesos de tratamiento son completamente diferentes, al igual que las características superficiales y los sectores de aplicación.
El niquelado electrolítico se utiliza principalmente, pero no solo, en el campo decorativo, para dar resistencia a la corrosión y un aspecto metálico plateado. Por lo general, se combina con un recubrimiento de cobre subyacente con el fin de aumentar la adherencia y dar un aspecto lustroso y brillante. Tiene una dureza media y una escasa resistencia a la corrosión.
En cambio, el niquelado químico se elige en el ámbito técnico para aumentar la dureza hasta 1000 HV, incrementar la resistencia al desgaste, reducir el coeficiente de fricción y proporcionar una excelente resistencia a la corrosión. Es aplicable a todas las aleaciones de hierro, aluminio, cobre y titanio.
Normas técnicas de referencia
Las normas técnicas y los estándares internacionales relacionados con el níquel químico son los siguientes:
Norma / Estándar | Título |
---|---|
ISO 4527 | Metallic coatings - Autocatalytic (electroless) nickel-phosphorus alloy coatings - Specification and test methods |
ASTM B733 | Standard Specification for Autocatalytic (Electroless) Nickel-Phosphorus Coatings on Metal |
MIL-C-26074 | Coatings, Electroless Nickel, Requirement for |
AMS C26074 | Electroless Nickel Coatings |
AMS 2404 | Plating, Electroless Nickel |
AMS 2405 | Electroless Nickel Plating Low Phosphorus |
La norma más utilizada y reconocida es la ISO 4527, que define los requisitos y métodos de prueba para los recubrimientos químicos autocatalíticos de aleación de níquel-fósforo aplicados sobre sustratos metálicos a partir de soluciones acuosas.
Tipos de níquel químico
Los recubrimientos se distinguen según la cantidad de fósforo presente en la aleación:
% de fósforo | Tipo de niquelado químico | Info |
---|---|---|
1-4 % P | Níquel químico de bajo contenido en fósforo | Poco utilizado industrialmente |
5-9 % P | Níquel químico de medio contenido en fósforo Niplate 600 | Se prefiere por su mayor dureza y resistencia al desgaste, así como por su menor coste |
>10 % P | Níquel químico de alto contenido en fósforo Niplate 500 | Se prefiere por su mayor resistencia a la corrosión |
Con el fin de aumentar las propiedades superficiales de los recubrimientos de níquel químico, se han desarrollado recubrimientos que contienen partículas con propiedades especiales, por ejemplo:
- Níquel químico + PTFE: las partículas nanométricas de PTFE se codepositan dentro de la capa de níquel químico en una concentración de 25-35 % en volumen. Gracias a las propiedades del PTFE, el recubrimiento de Niplate 500 PTFE tiene un coeficiente de fricción muy bajo (0,08-0,10) con una alta resistencia a la corrosión, una buena dureza y una excelente adherencia al metal base, una característica que a menudo falta en los recubrimientos de PTFE por pulverización.
- Níquel químico + SiC: para aplicaciones en las que la resistencia al desgaste es la máxima prioridad, se ha desarrollado el recubrimiento compuesto Niplate 600 SiC . Las partículas micrométricas de carburo de silicio (SiC), material cerámico de elevada dureza, confieren al recubrimiento de níquel químico una resistencia excepcional al desgaste tanto abrasivo como adhesivo, superior al cromado.
Aspecto estético
El níquel químico tiene un aspecto metálico brillante de color similar al acero inoxidable. Presenta una alta resistencia a la oxidación y, por lo tanto, mantiene el color y el brillo durante mucho tiempo.
La morfología superficial de la pieza y la rugosidad no se ven alteradas por el recubrimiento y, por lo tanto, el aspecto estético final es igual al inicial.
Se puede obtener un acabado mate mediante los procesos de arenado, «shot peening» o granallado.
El níquel químico + PTFE tiene un color gris «cañón de fusil».
El níquel químico + SiC tiene un color gris claro.
Aleaciones metálicas recubribles
El niquelado químico se puede aplicar a la mayoría de las aleaciones comúnmente utilizadas en el ámbito mecánico:
- Acero al carbono
- Acero inoxidable
- Aceros cementados, templados y nitrurados
- Aleaciones de aluminio, extruidas, laminadas, fundidas y fundidas a presión.
- Aleaciones de cobre y latón
- Aleaciones de titanio
Espesor de recubrimiento y tolerancia
El espesor del recubrimiento de níquel químico es uniforme en toda la superficie de la pieza.
Se utilizan espesores de recubrimiento comprendidos entre 5 y 50 µm, con una tolerancia de ±10 % y un valor mínimo de ± 2µm. Los espesores estándar son los siguientes:
- 5±2 µm
- 10±2 µm
- 20±2 µm
Para algunas aplicaciones exigentes de desgaste o resistencia a la corrosión, como, por ejemplo, el ambiente marino, se pueden elegir espesores de 30±3 µm o 50±5 µm, que permiten aumentar la resistencia proporcionalmente al espesor.
La elección del espesor ideal debe evaluarse en función de los requisitos, del material base y de las condiciones de uso, como, por ejemplo, el desgaste o la agresividad del ambiente. Micron Srl está disponible para ayudar a los ingenieros, diseñadores y talleres mecánicos en la elección y definición del espesor correcto.
Dureza y tratamientos térmicos de endurecimiento
El recubrimiento de niquelado químico tiene una dureza muy alta, mayor que casi todas las demás aleaciones metálicas. Los tratamientos térmicos realizados en los recubrimientos de níquel químico permiten aumentar significativamente la dureza, logrando una dureza igual a 1000 HV (69 HRC) que supera la dureza del acero cementado o nitrurado. Esto permite aumentar significativamente la resistencia al desgaste de los componentes recubiertos, gracias también al bajo coeficiente de fricción del níquel químico.
Deshidrogenación
Durante el proceso de niquelado químico se produce una difusión de hidrógeno atómico dentro de la matriz metálica, tanto en el recubrimiento como en el sustrato. Los aceros de alta resistencia, debido a este fenómeno, pueden manifestar la llamada fragilización por hidrógeno. Durante el niquelado químico, dado que la deposición del metal se produce sin suministro de corriente, el contenido de hidrógeno que se puede difundir en el metal es significativamente menor que durante los recubrimientos metálicos galvánicos tradicionales, como el cromado o el niquelado electrolítico. Por lo general, se realiza un tratamiento térmico llamado deshidrogenación a 180 °C durante 4 horas, que permite eliminar el hidrógeno y mejorar la adhesión del recubrimiento.
Endurecimiento
Los tratamientos térmicos de endurecimiento, que permiten aumentar la dureza del recubrimiento, se realizan generalmente a una temperatura de 260-280 °C para una dureza de aproximadamente 800 HV, y a 340 °C para una dureza de aproximadamente 1000 HV. El tratamiento térmico a 260-280 °C puede provocar una ligera coloración amarilla de la superficie de las piezas debido a una ligera oxidación de la superficie que se produce a esas temperaturas. El tratamiento de endurecimiento a 340 °C se realiza habitualmente en horno de aire y provoca una coloración amarilla-azul iridiscente en la superficie de las piezas. El mismo tratamiento de endurecimiento se puede realizar, alternativamente, en un horno en una atmósfera controlada que permite mantener el aspecto metálico del níquel químico.
Resistencia a la corrosión
El niquelado químico es un recubrimiento que proporciona una excelente resistencia a la corrosión. El comportamiento frente a la corrosión depende en gran medida de la aleación metálica recubierta y, por este motivo, es conveniente hacer algunas aclaraciones.
En las aleaciones de hierro se obtiene la mejor resistencia a la corrosión con los tratamientos de galvanizado, ya que el zinc es sacrificial y se corroe primero, evitando la corrosión del hierro. El níquel químico se elige en sustitución del galvanizado cuando es necesario proteger también las zonas internas, respetar tolerancias estrictas, tener una mejor adherencia, resistencia al desgaste y a los arañazos, así como cuando la pieza está en contacto con sustancias ligeramente ácidas o alcalinas.
En las aleaciones de aluminio el níquel químico compite con la anodización, diferenciándose por una mayor dureza superficial, una mejor resistencia química en entornos no neutros, un menor coeficiente de fricción y rugosidad, conductividad eléctrica y recubrimiento de todas las superficies, incluidas las internas.
En las aleaciones de cobre (latón), el niquelado químico proporciona una excelente resistencia a la corrosión, logrando alcanzar hasta 1000 horas de niebla salina neutra NSS sin que aparezca ningún tipo de corrosión.
El níquel químico tiene una excelente resistencia química en contacto con ambientes neutros o ligeramente agresivos, se oxida con dificultad y conserva el aspecto metálico superficial. Resiste bien el contacto con hidrocarburos, alcohol, soluciones salinas neutras, ácidos reductores diluidos y bases diluidas. Tiene dificultades en contacto con ácidos y bases concentrados, especialmente oxidantes.
Magnetismo
El níquel químico de medio contenido en fósforo es ferromagnético, es decir, tiene la capacidad de magnetizarse bajo la acción de un campo magnético externo. El níquel químico de alto contenido en fósforo no es ferromagnético, aunque comienza a exhibir propiedades ferromagnéticas si se somete a temperaturas superiores a 250 °C. Por este motivo, si se necesita ausencia de magnetismo, se debe elegir el niquelado químico de alto contenido en fósforo Niplate 500 sin tratamientos de endurecimiento.
Rugosidad
El niquelado químico no altera la rugosidad superficial del procesamiento mecánico y, por lo tanto, es posible mantener los valores casi inalterados.
Rectificación
Algunas aplicaciones particulares requieren un rectificado después del recubrimiento de níquel químico, como, por ejemplo, los vástagos oleohidráulicos que requieren tolerancias muy estrictas y acoplamientos precisos.
El níquel químico, a pesar de ser muy duro, se presta a ser rectificado con bastante facilidad. Incluso se prefiere el tratamiento de endurecimiento a 800 HV o 1000 HV, ya que resulta mejor la procesabilidad y la capacidad de eliminación de las virutas.
Soldabilidad
El níquel químico Niplate se presta fácilmente a ser soldado. Se utiliza ampliamente en conductores de cobre con el fin de evitar la oxidación superficial y permitir una excelente soldabilidad de los componentes electrónicos. El níquel químico, además de proteger al cobre contra la corrosión, mantiene inalteradas las características superficiales a lo largo del tiempo, ya que no se oxida ni se corroe.
REACH y RoHS
Los recubrimientos de niquelado químico Niplate cumplen con el reglamento REACH y la directiva RoHS, ya que no hay sustancias con restricciones de uso —más allá de las concentraciones máximas toleradas— y tampoco hay SVHC en cantidades superiores al 0,1 % en peso.