L’anodisation (également appelée oxydation anodique) est un processus électrochimique qui permet d’obtenir sur la surface métallique de la pièce traitée une couche compacte d’oxyde. Ce processus utilise le courant électrique et son nom vient du fait que la pièce à traiter est connectée à l’anode d’une cellule électrolytique.
L’anodisation est le principal traitement protecteur effectué sur l’aluminium. D’autres métaux qui peuvent être facilement anodisés sont le titane et le magnésium.
Anodisation de l’aluminium
Le premier processus d’anodisation, développé dans les années 1920-1930, était à base d’acide chromique. Ce revêtement, appelé anodisation chromique, n’est maintenant effectué que pour certains secteurs spécifiques tels que l’armée et l’aéronautique, en raison de la cancérogénicité des sels de chrome.
Actuellement, le processus d’anodisation le plus répandu et le plus utilisé est celui à base d’acide sulfurique.
Les pièces à usiner sont immergées dans une solution d’acide sulfurique à 20 % qui sert d’électrolyte. Le pôle positif est appliqué à la pièce en aluminium tandis que le pôle négatif est connecté à une cathode présente dans la solution. En appliquant du courant à la cellule électrolytique, des ions oxygène se développent sur la surface de la pièce à usiner qui, en se combinant avec les atomes d’aluminium, forment une couche dure et compacte d’oxyde d’aluminium avec d’excellentes caractéristiques de :
- résistance à la corrosion
- résistance à l’usure
- dureté
- uniformité d’épaisseur
- possibilité de coloration avec des pigments qui pénètrent la couche d’oxyde
- isolation diélectrique
Structure de la couche d’oxyde
L’oxyde d’aluminium, formé par le processus d’anodisation en acide sulfurique, a une structure en colonnes en nid d’abeille, avec des cellules de forme hexagonale et avec une porosité centrale qui s’étend sur presque toute la profondeur. Le processus d’anodisation dure forme la porosité avec un diamètre d’environ 20-40 nm et une distance entre les pores et des pores d’environ 100 nm.
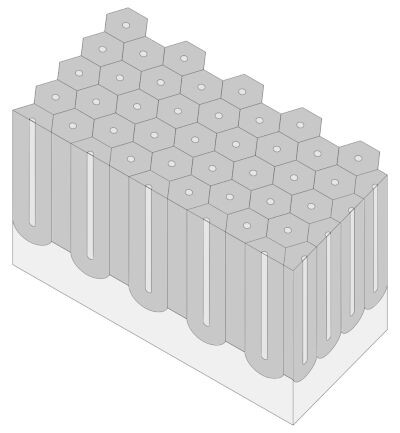
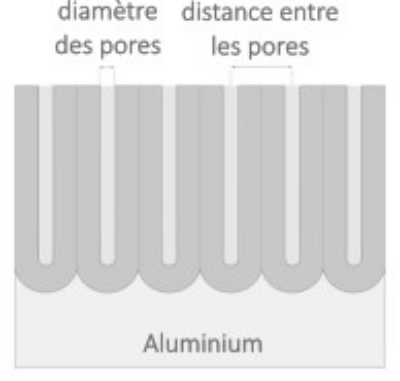
Il existe deux types d’anodisation, avec différentes caractéristiques de surface et différents paramètres de traitement :
Type d’anodisation | Caractéristiques |
---|---|
Anodisation naturelle ou décorative OX-A | Utilisée pour fournir une bonne résistance à la corrosion dans des environnements non agressifs et une résistance discrète à l’usure et aux rayures. Utilisée dans le domaine de la décoration car elle se prête à être colorée en différentes couleurs. |
Anodisation dure OX-HS - OX-W | Utilisée sur les pièces de mécanique de précision pour conférer une excellente résistance à la corrosion et à l’usure, une dureté élevée et une résistance dans les environnements agressifs. |
Anodisation dure de l’aluminium
Avec le terme anodisation dure, un revêtement en oxyde d’aluminium très dur et compact est identifié, avec des épaisseurs plus élevées que l’anodisation décorative. Elle est principalement utilisée dans la mécanique de précision sur les pièces usinées mécaniquement dans la masse, sur les pièces extrudées, sur les pièces moulées, moulées sous pression et laminées dans le but d’augmenter la résistance à la corrosion, la dureté et la résistance à l’usure.
Normes techniques de référence
Les normes techniques et les normes internationales relatives à l’anodisation dure sont les suivantes :
Norme / Standard | Titre |
---|---|
ISO 10074 | Anodizing of Aluminium and its alloys - Specification for hard anodic oxidation coatings on Aluminium and its alloys |
MIL-A-8625 | ANODIC COATINGS FOR ALUMINUM & ALUMINUM ALLOYS - Type III: Hard Anodic Coatings |
UNI 7796 | Revêtements pour l’oxydation anodique de l’aluminium et des alliages d’aluminium - Oxydation anodique épaisse - Exigences et instructions générales de contrôle |
Aspect esthétique
L’anodisation dure reprend la morphologie de surface de la pièce et il est donc possible de maintenir les finitions de surface de l’aluminium même après l’anodisation (par exemple brillante, satinée, brossée, grenaillée, granulée, sablée, etc.)
Le revêtement prend une auto-coloration qui dépend beaucoup de l’alliage d’aluminium utilisé et peut varier entre le gris, le gris foncé et le brun. Après le traitement, la surface peut être pigmentée avec du colorant noir, bleu ou rouge. Ces pigments pénètrent à l’intérieur de la couche d’anodisation, ce qui la colore. Comme la couleur de base de la couche anodisée est de couleur foncée, contrairement aux traitements d’anodisation naturelle, les traitements d’anodisation dure prennent une couleur noir profond, bleu foncé et rouge foncé. L’épaisseur affecte ce qui rend le revêtement plus sombre lorsque l’épaisseur augmente. Les alliages contenant beaucoup de cuivre acquièrent un aspect bronze et les alliages contenant beaucoup de silicium (>12 %) pourraient avoir une couleur hétérogène. L’anodisation dure, qui a une couleur de couleur foncée, se prête à être colorée avec des couleurs sombres et couvrantes et la couleur noire est généralement choisie, à la fois pour son excellent rendement esthétique et pour uniformiser la couleur en présence de différents alliages.
Alliages d’aluminium anodisables
Tous les alliages d’aluminium sont anodisables, à quelques exceptions près. Les plus grandes difficultés sont rencontrées pour les alliages qui contiennent des éléments autres que l’aluminium en grande quantité, car seul l’aluminium contribue à la formation de la couche d’oxyde. Il en résulte que les alliages contenant de grandes quantités de cuivre tels que la série 2000 ne peuvent pas atteindre une épaisseur élevée et que la couche d’oxyde sera légèrement moins compacte et moins résistante à la corrosion et à l’usure. Les alliages contenant plus de 12 % de silicium peuvent présenter une épaisseur et une uniformité de revêtement inférieures, ce qui réduit la résistance à la corrosion, l’usure et parfois les différences de couleur.
Épaisseurs d’anodisation
Une caractéristique particulière de l’anodisation est la possibilité de recouvrir les pièces avec une épaisseur uniforme et calibrée sur presque toutes les surfaces. Les orifices de petit diamètre et très profonds peuvent faire exception, car leur capacité de pénétration du revêtement doit être évaluée individuellement.
L’épaisseur standard de l’anodisation dure est de 30 à 50 µm, mais des épaisseurs inférieures ou supérieures peuvent être sélectionnées en fonction des besoins spécifiques. En présence de tolérances très étroites, l’épaisseur d’anodisation a tendance à diminuer et/ou à définir une tolérance plus étroite telle que 30±5 µm.
Croissance dimensionnelle
L’épaisseur de traitement croît de 50 % à l’extérieur et de 50 % à l’intérieur de la surface de la pièce en aluminium. L’augmentation dimensionnelle radiale est donc égale à la moitié de l’épaisseur de traitement.
Résistance à la corrosion
L’anodisation dure a une résistance à la corrosion plus importante que l’anodisation décorative, grâce à la plus grande épaisseur et à la plus grande compacité de la couche d’oxyde. Cette résistance peut être affectée par la porosité présente dans le revêtement, qui est le premier déclencheur de la corrosion. Pour augmenter la résistance à la corrosion, un traitement ultérieur à l’anodisation est ensuite effectué, appelé fixation. Il existe différents types de fixation et les deux plus utilisés industriellement et reconnus au niveau international sont :
- fixation à chaud : immersion dans l’eau à une température d’environ 95 °C, ce qui permet une hydratation superficielle de la couche d’oxyde d’aluminium et ferme les porosités, permettant ainsi une meilleure résistance à la corrosion.
- fixation à froid : immersion dans une solution de nickel fluorure à température ambiante. Les sels de nickel pénètrent dans la porosité du revêtement en améliorant la résistance à la corrosion.
La fixation à chaud, bien que coûteuse en énergie car elle doit être maintenue à 95 °C, est de plus en plus utilisée, au détriment de celle à base de sels de nickel, qui sont cancérigènes et peuvent provoquer des allergies cutanées. Dans le domaine alimentaire, par exemple, la fixation à base de nickel ne peut pas être utilisée.
L’anodisation résiste parfaitement à la corrosion au contact des alcools, des hydrocarbures et des solutions neutres. Des solutions acides ou basiques dissolvent l’oxyde d’aluminium en annulant l’effet barrière de protection contre la corrosion. La vitesse de dissolution de la couche d’anodisation est proportionnelle à l’acidité ou à la basicité de la solution et plus élevée en cas de solution de base.
L’anodisation dure OX-W est un traitement spécialement développé pour augmenter la résistance à la corrosion déjà excellente de l’anodisation dure. Sur certains alliages, il permet d’atteindre 1000 heures d’exposition au brouillard salin neutre selon la norme ISO 9227, sans apparition de corrosion. OX-W convient également à la protection des alliages à haute teneur en silicium, qui, avec le processus d’anodisation standard, pourraient rencontrer des difficultés.
Dureté, densité et résistance à l’usure
L’anodisation dure a une dureté élevée, qui varie en fonction de l’alliage d’aluminium utilisé.
La spécification ISO 10074 établit la dureté minimale que doivent avoir certains alliages. La dureté est mesurée conformément à la norme ISO 4516 sur une couche d’épaisseur comprise entre 25 et 50 µm et avec une charge de 50 g HV 0,05.
Alliage | Dureté Vickers |
---|---|
Alliages d’usinage plastique | 400 HV |
Série 2000 | 250 HV |
Série 5000 avec magnésium >2 % | 300 HV |
Série 7000 | 300 HV |
Alliages de fusion avec cuivre <2 % et/ou silicium <8 % | 250 HV |
La densité, mesurée conformément à la norme ISO 2106 sur un revêtement de 50 µm ± 5 µm sans fixation, doit avoir les valeurs minimales suivantes :
Alliage | Densité du revêtement |
---|---|
Alliages d’usinage plastique | 1100 mg/dm2 |
Série 2000 | 950 mg/dm2 |
Série 5000 avec magnésium >2 % | 950 mg/dm2 |
Série 7000 | 950 mg/dm2 |
Alliages de fusion avec cuivre <2 % et/ou silicium <8 % | 950 mg/dm2 |
La dureté et la compacité élevées de la couche d’oxyde et la structure en colonnes permettent à l’anodisation dure d’atteindre une résistance élevée à l’usure, supérieure au nickelage chimique et comparable au chromage dur à épaisseur. Le Taber Abraser est un test qui détermine l’usure des revêtements à glissement sur roues abrasives. Selon la norme ISO 10074, après 10 000 cycles, la perte de masse doit être inférieure aux valeurs suivantes :
Alliage | perte de poids maximale |
---|---|
Alliages d’usinage plastique | 15 mg |
Série 2000 | 35 mg |
Série 5000 avec magnésium >2 % | 25 mg |
Série 7000 | 25 mg |
Alliages de fusion avec cuivre <2 % et/ou silicium <8 % | - |
Rugosité
L’anodisation dure contribue à augmenter légèrement la rugosité de surface et est plus visible sur les surfaces avec une faible rugosité par usinage mécanique.
L’anodisation dure OX-W a comme caractéristique de contenir l’augmentation de la rugosité de surface. Grâce à l’utilisation de certains alliages d’aluminium spécifiques et à la définition des paramètres de fonctionnement corrects, il est possible de maintenir la rugosité finale à des valeurs inférieures à 0,5 Ra.
Contact alimentaire
La norme “EN 14392 Requirements for anodized products for use in contact with foodstuff” spécifie les exigences des traitements d’anodisation sur des pièces en aluminium destinées au contact alimentaire.
Les traitements effectués par Durox srl sont conformes à la norme EN 14392 si les exigences suivantes sont respectées :
- La composition chimique des alliages d’aluminium des pièces à anodiser doit être conforme aux exigences des normes EN 601 ou EN 602, le cas échéant.
- Les traitements d’anodisation doivent subir la phase de fixation qui doit être expressément demandée.