L’anodisation de l’aluminium , également appelée oxydation anodique, est un processus électrolytique par lequel une couche d’oxyde d’aluminium se forme sur la surface de la pièce à usiner, ce qui confère d’excellentes caractéristiques de surface à la pièce usinée.
Le processus d’anodisation de l’aluminium le plus largement utilisé industriellement est effectué par l’utilisation d’une solution d’acide sulfurique comme électrolyte. Il existe également un processus d’anodisation appelé anodisation chromique, qui utilise une solution d’acide chromique comme électrolyte. Ce revêtement est peu utilisé dans le domaine industriel car l’acide chromique est cancérigène et est principalement utilisé dans le domaine militaire et aéronautique. Les pièces à usiner sont immergées dans une cuve contenant de l’électrolyte, le courant anodique est appliqué à la pièce (d’où le nom “anodisation”) et le courant cathodique sur les côtés de la cuve. Le processus avec de l’acide sulfurique est considéré comme “respectueux de l’environnement” car aucune substance telle que des métaux lourds, des solvants ou des substances cancérigènes n’est utilisée.
PRINCIPALES CARACTÉRISTIQUES
L’anodisation est le revêtement le plus utilisé et le plus apprécié sur l’aluminium car il confère d’excellentes propriétés de surface aux pièces recouvertes, avec des coûts assez faibles.
Ses principales caractéristiques sont :
- résistance à la corrosion
- résistance à l’usure
- dureté
- uniformité d’épaisseur
- isolation diélectrique
- possibilité de coloration avec des pigments qui pénètrent la couche d’oxyde.
ALLIAGES ANODISABLES
La plupart des alliages d’aluminium généralement utilisés en mécanique peuvent être anodisés facilement et avec d’excellents résultats.
Les caractéristiques du revêtement peuvent différer en fonction de l’alliage utilisé, car il s’agit d’un processus de transformation de l’aluminium en oxyde d’aluminium, la composition de l’alliage peut donc modifier ses caractéristiques.
Les plus grandes difficultés sont rencontrées pour les alliages qui contiennent des éléments autres que l’aluminium en grande quantité, car seul l’aluminium contribue à la formation de la couche d’oxyde. Il en résulte que les alliages contenant de grandes quantités de cuivre tels que la série 2000 ne peuvent pas atteindre une épaisseur élevée et que la couche d’oxyde sera légèrement moins compacte et moins résistante à la corrosion et à l’usure. Les alliages contenant plus de 10 % de silicium peuvent présenter des différences de couleur et ne pas atteindre une épaisseur élevée.
TYPES D’ANODISATION
On peut distinguer deux types différents d’anodisation en acide sulfurique, qui diffèrent à la fois par leurs caractéristiques de surface et par le processus avec lequel ils sont effectués :
- Anodisation naturelle, telle que l’anodisation OX-A
- Anodisation dure, telle que l’anodisation OX-HS et OX-W
Les différences de la couche anodique et de ses caractéristiques de surface sont dues à l’utilisation de différents paramètres de fonctionnement tels que la température de l’électrolyte et le courant appliqué (volts et ampères). Les installations au service du processus d’oxydation anodique sont également différentes pour les deux types.
ANODISATION NATURELLE
L’anodisation naturelle, également appelée anodisation décorative, est principalement utilisée à des fins décoratives ou de protection dans des environnements peu agressifs.
Elle est de couleur gris clair et se prête très bien à la coloration grâce à l’utilisation de pigments qui pénètrent la couche d’oxyde, garantissant ainsi un excellent rendu des couleurs ainsi qu’une résistance aux rayures et aux décolorations.
ANODISATION DURE
L’anodisation dure améliore et augmente les caractéristiques de l’anodisation naturelle grâce à une couche d’oxyde très dense et compacte avec une dureté élevée et une excellente résistance à la corrosion. Ce traitement est principalement utilisé dans les applications mécaniques pour lesquelles une excellente résistance à l’usure est requise et dans les environnements industriels ou marins caractérisés par des agents agressifs.
NORMES DE RÉFÉRENCE
Les principales normes techniques et les normes internationales relatives à l’anodisation sont les suivantes :
Anodisation naturelle
Norma | Titre |
---|---|
ISO 7599 | Anodizing of Aluminium and its alloys Method for specifying decorative and protective anodic oxidation coatings on Aluminium |
UNI 10681 | _ Aluminium et alliages d’aluminium_ caractéristiques générales des couches d’oxyde anodique à usage décoratif et protecteur |
MIL-PRF-8625, Type II | ANODIC COATINGS FOR ALUMINUM & ALUMINUM ALLOYS Type II: Sulfuric acid anodizing, conventional coatings produced from sulfuric acid bath |
Anodizzazione dure
Norma | Titre |
---|---|
ISO 10074 | Anodizing of Aluminium and its alloys Specification for hard anodic oxidation coatings on Aluminium and its alloys |
UNI 7796 | Revêtements pour l’oxydation anodique de l’aluminium et des alliages d’aluminium Oxydation anodique épaisse - Exigences et instructions générales de contrôle |
MIL-PRF-8625, Type III | ANODIC COATINGS FOR ALUMINUM & ALUMINUM ALLOYS Type III: Hard Anodic Coatings |
ÉPAISSEUR D’ANODISATION
CLASSE SELON LA NORME 7599 | ÉPAISSEUR MOYENNE MINIMALE |
---|---|
AA 5 | 5 µm |
AA 10 | 10 µm |
AA 15 | 15 µm |
AA 20 | 20 µm |
AA 25 | 25 µm |
SPÉCIFIQUE | ÉPAISSEUR NOMINALE |
---|---|
ISO 10074 | 40 – 60 µm |
MIL-PRF-8625 | ≃ 40 – 60 µm (2” ± 20%) |
UNI 7796 | 30 – 60 µm |
CALCUL DIMENSIONNEL
Pour mieux comprendre la croissance de l’épaisseur de l’anodisation, afin de calculer correctement la taille, il est nécessaire de comprendre le mécanisme de formation de la couche d’anodisation.
Comme nous l’avons dit précédemment, l’anodisation est un processus qui transforme l’aluminium en oxyde d’aluminium en formant une couche qui peut avoir différentes épaisseurs.
La croissance de l’oxyde d’aluminium entraîne inévitablement une décroissance de l’aluminium métallique qui se transforme en oxyde. Il faut donc veiller à ne pas considérer l’épaisseur de l’anodisation comme un “surmétal”, mais il est nécessaire de savoir à quel pourcentage le revêtement “pénètre” et de combien est sa “croissance”.
En mécanique de précision, les tolérances sont très étroites et le concepteur peine à les définir lorsqu’il y a des revêtements appliqués, car les tolérances de traitement s’ajoutent à celles du revêtement. La définition précise et correcte des cotes finales et des tolérances du revêtement devient donc d’une importance fondamentale, afin d’éviter les erreurs, qui pourraient entraîner des écarts ou des retouches.
Dans les applications d’anodisation naturelle, en particulier décoratives, on considère à tort que l’anodisation ne crée pas de croissance dimensionnelle.
Dans de telles applications, les tolérances ne sont pas critiques et il est plus facile de supposer qu’il n’y a pas de croissance.
En vérité, l’épaisseur de l’oxyde crée une croissance dimensionnelle d’environ 30 % de l’épaisseur de l’anodisation, qui est généralement de 10 µm, créant ainsi une croissance de seulement 3 µm.
Une autre variable qui peut affecter légèrement les cotes finales est due au traitement de nettoyage préalable à l’anodisation, appelé décapage alcalin, qui dissout légèrement l’aluminium de surface, diminuant ainsi la cote finale. Cette valeur ne peut pas être définie de manière standard car elle dépend du temps passé dans ce réservoir et de sa concentration. Il peut être de quelques microns dans le cas de composants de mécanique de précision à quelques centièmes de millimètre sur des pièces extrudées pour lesquelles vous souhaitez supprimer les lignes d’extrusion.
ANODISATION NATURELLE
Le revêtement croît de 30 % à l’extérieur et de 70 % à l’intérieur de la surface de la pièce en aluminium.
L’augmentation dimensionnelle radiale est donc égale à 30 % de l’épaisseur de traitement.
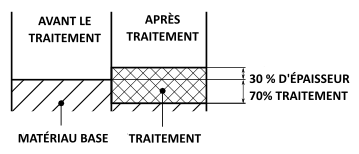
ANODISATION DURE
L’épaisseur de traitement croît de 50 % à l’extérieur et de 50 % à l’intérieur de la surface de la pièce en aluminium.
L’augmentation dimensionnelle radiale est donc égale à la moitié de l’épaisseur de traitement.
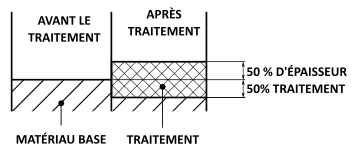
CALCULATEUR DE COTES
Pour aider les concepteurs et les ateliers mécaniques à définir les cotes et les tolérances en présence de revêtements tels que l’anodisation et le nickelage chimique, nous avons développé un calculateur automatique des tolérances dimensionnelles de prétraitement. Il suffit d’entrer les tolérances, le type de traitement avec son épaisseur et le calculateur génère automatiquement les tolérances d’usinage mécanique de prétraitement pour avoir les cotes finales tolérées correctes.