L’anodisation dure de l’aluminium est un processus qui permet de créer sur la surface du matériau une couche d’oxyde d’aluminium avec des propriétés de dureté et de résistance à l’usure supérieures à celles de l’anodisation naturelle ou architecturale.
Cela est dû au fait que la couche d’anodisation dure est plus épaisse et est obtenue en utilisant différents paramètres de traitement, tels que la température de l’électrolyte d’anodisation, qui pour l’anodisation dure est d’environ 0 °C, contre 20 °C pour l’anodisation architecturale. De cette façon, vous obtenez un revêtement dur et résistant à l’usure, adapté à différents types d’applications.
La dureté
Comme mentionné précédemment, l’anodisation dure présente une dureté élevée, qui dépend de l’alliage d’aluminium utilisé. En général, la dureté des traitements d’anodisation varie de 280 à 500 HV, en fonction de l’alliage choisi. Par exemple, les alliages d’aluminium de la série 6000 sont particulièrement adaptés pour obtenir des couches d’anodisation dure de dureté élevée, tandis que les alliages de la série 2000, en raison de leur teneur en cuivre, atteignent des valeurs de dureté inférieures, environ 280 HV. Les alliages de la série 7000 se placent à moitié et peuvent atteindre une dureté d’environ 350 HV.
La résistance à l’usure
La résistance à l’usure des revêtements d’anodisation dure est une propriété étroitement liée à la dureté du traitement. Plus la dureté est élevée, plus la résistance à l’usure est élevée. Pour mesurer la résistance à l’usure des revêtements d’anodisation dure, le test de résistance à l’abrasion Taber Abraser, qui consiste à effectuer un test d’abrasion sur une éprouvette en frottant avec des roues abrasives, est couramment utilisé. La résistance à l’abrasion est calculée en fonction de la réduction de poids de l’éprouvette avant et après le test, qui consiste en 10 000 cycles d’abrasion.
Selon les résultats obtenus avec le test Taber Abraser, les alliages d’aluminium de la série 6000 présentent les plus grandes résistances à l’abrasion, suivis des alliages de la série 7000. Au contraire, les alliages de la série 2000 présentent les résistances à l’usure les plus faibles. Cependant, il est important de souligner que la résistance à l’usure des revêtements d’anodisation dure est généralement très élevée, supérieure à celle des alliages d’acier et du nickelage chimique, et comparable à celle du chrome dur.
Applications pour la résistance à l’usure
En plus de conférer une grande résistance à la corrosion, les traitements d’anodisation dure sont utilisés pour augmenter la résistance à l’usure des alliages d’aluminium.
Dans le secteur automobile, par exemple, l’anodisation dure est souvent appliquée à des composants mécaniques tels que des corps de vanne, des tiges et des flotteurs, qui peuvent être soumis à des frottements et à des abrasions lors de leur utilisation. Grâce à la dureté et à la résistance à l’usure de la surface anodisée, ces composants ont une durée de vie plus longue. Dans le secteur des vélos, l’anodisation dure est utilisée, par exemple, sur des couronnes pour résister à l’abrasion causée par le passage de la chaîne. En outre, dans le secteur des machines industrielles, l’anodisation dure est souvent appliquée à des rouleaux de transfert de machines d’impression ou de conditionnement pour réduire l’usure causée par le frottement avec du papier ou d’autres matériaux. Même dans le secteur textile, différentes parties sont traitées avec une anodisation dure pour résister à l’usure due au frottement avec d’autres parties ou avec la fibre textile.
Conclusions
En résumé, l’anodisation dure est un traitement de surface qui permet de conférer aux alliages d’aluminium des propriétés de dureté et de résistance à l’usure supérieures à celles de l’anodisation naturelle ou architecturale. La dureté des revêtements d’anodisation dure varie en fonction de l’alliage d’aluminium utilisé, mais elle est généralement comprise entre 280 et 500 HV. La résistance à l’usure est mesurée avec le test de résistance à l’abrasion Taber Abraser et dépend également de l’alliage choisi. En général, les alliages des séries 6000 et 7000 présentent les plus grandes résistances à l’abrasion, tandis que les alliages de la série 2000 présentent les résistances à l’usure les plus faibles. Cependant, il est important de souligner que la résistance à l’usure des revêtements d’anodisation dure est généralement très élevée et supérieure à celle des alliages d’acier et du nickelage chimique.
L’anodisation dure est utilisée dans différents secteurs industriels, tels que l’automobile, le secteur des vélos, le secteur des machines industrielles et le secteur textile, pour augmenter la durée de vie et la résistance à l’usure des composants soumis à des frottements et à des abrasions. De cette façon, l’anodisation dure représente une solution efficace pour améliorer les performances et la durée de vie de nombreux produits.
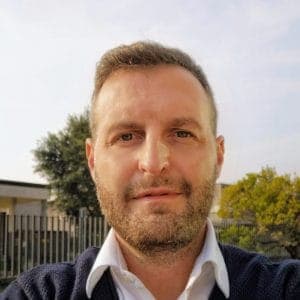