Différence entre le nickelage chimique et les revêtements galvaniques
Les revêtements galvaniques (par exemple, le chromage, le nickelage électrolytique, le zingage, le zinc-nickel) sont déposés en utilisant un courant continu appliqué à la pièce, ce qui permet le dépôt du métal sur la surface de la pièce à revêtir.
Le courant appliqué a tendance à se décharger en suivant le chemin à moindre résistance et, par conséquent, l’épaisseur du revêtement galvanique est plus grande sur les surfaces extérieures des pièces et sur les bords, et elle est moindre ou même manquante sur les cavités internes lorsque la pièce recouverte est assez complexe.
Le nickelage chimique est au contraire un processus de dépôt d’un alliage de nickel et de phosphore qui se produit par une réaction chimique d’oxydo-réduction, sans utilisation de courant. La caractéristique principale est de revêtir toutes les surfaces de la pièce avec une épaisseur uniforme et calibrée.
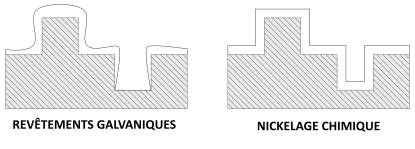
Mode de protection contre la corrosion Il existe deux types de comportement du revêtement qui affectent la résistance à la corrosion de la pièce recouverte :
- effet sacrificiel
- effet barrière
EFFET SACRIFICIEL
Il s’agit de la protection la plus fréquente contre la corrosion des revêtements à base de zinc et de nickel-zinc. Le zinc a une valeur de potentiel électrochimique inférieure au fer et devient donc sacrificiel en se corrodant en premier et en évitant la corrosion du fer. Ce n’est que lorsque le zinc sera presque complètement dissous, laissant des zones découvertes, que la corrosion du fer commencera, et qu’il progressera rapidement. Un exemple typique de corrosion sacrificielle est l’anode en magnésium insérée dans les bouilloires domestiques qui empêche la corrosion de l’acier car le magnésium est sacrificiel. Un autre exemple sont les anodes en zinc ou en magnésium utilisées sur les coques des bateaux. C’est pour cette raison que, pour évaluer la résistance à la corrosion des pièces galvanisées, le temps écoulé avant l’apparition de produits de corrosion blancs (oxyde de zinc) et l’apparition de produits de corrosion rouges (oxyde de fer) sont pris en compte. Un exemple d’exigence typique (pour la galvanisation) de résistance à la corrosion après exposition au brouillard salin neutre selon la norme ISO 9227 est : 96 heures sans apparition de corrosion blanche et 168 heures sans apparition de corrosion rouge.
EFFET BARRIÈRE
L’alliage de nickel phosphore déposé par le procédé de nickelage chimique a un potentiel électrochimique plus élevé que le fer et l’aluminium et n’est donc pas sacrificiel par rapport à ces derniers. Il agit comme une protection contre la corrosion car il forme une couche barrière qui exerce une action d’imperméabilisation contre les agents agressifs externes. L’alliage de nickel phosphore a une résistance chimique élevée et n’est presque pas corrodé par des solutions salines neutres, en particulier le Niplate 500 haut phosphore. C’est pour cette raison que, compte tenu du revêtement uniquement, il est possible d’atteindre des milliers d’heures d’exposition au brouillard salin sans corrosion. Cependant, il faut tenir compte du fait que toute imperfection éventuelle du revêtement peut générer de la corrosion du matériau sous-jacent, même après quelques heures d’exposition au brouillard salin. Les causes de ces imperfections peuvent être multiples, parmi ces causes nous pouvons citer :
- Porosité du revêtement due au processus même de nickelage ou aux inclusions/défauts dans le matériau de base ;
- Surfaces laissées brutes et donc caractérisées par des défauts de tréfilage et des inclusions superficielles ;
- Graisses, huiles et pâtes difficiles à éliminer ;
- Bords vifs et arrêtes ;
Pour le nickelage chimique, il n’est donc pas logique d’attribuer une limite à l’apparition de la rouille rouge, qui peut apparaître même après quelques heures d’exposition lorsque le revêtement présente un petit défaut. Le grand avantage du nickelage chimique est sa capacité à conserver la protection du substrat même après de nombreuses heures d’exposition au brouillard salin, ne présentant que quelques piqûres de corrosion initiales et par conséquent une très faible surface corrodée.
Un indice de protection est donc généralement attribué après exposition au brouillard salin pendant une durée déterminée par le concepteur, comme détaillé ci-dessous.
Évaluation de la résistance à la corrosion du nickelage chimique La résistance à la corrosion des articles recouverts de nickelage chimique est généralement évaluée par un test au brouillard salin neutre (NSS) selon les deux spécifications suivantes :
Norme | Description |
---|---|
ISO 9227 | Tests de corrosion en atmosphères artificielles - Tests au brouillard salin |
ASTM B117 | Standard Practice for Operating Salt Spray (Fog) Apparatus |
Suite au test au brouillard salin, l’évaluation de la résistance à la corrosion est réalisée à l’aide de la spécification UNI EN ISO 10289 - Évaluation des échantillons et des articles soumis à des tests de corrosion. Cette dernière attribue un indice de protection en fonction de la zone corrodée par rapport à la zone exposée au brouillard salin, comme résumé dans le tableau suivant :
Zone des défauts A (%) | Indice |
---|---|
Aucun défaut | 10 |
0 < A ≤ 0,1 | 9 |
0,1 < A ≤ 0,25 | 8 |
0,25 < A ≤ 0,5 | 7 |
0,5 < A ≤ 1 | 6 |
1 < A ≤ 2,5 | 5 |
2,5 < A ≤ 5 | 4 |
5 < A ≤ 10 | 3 |
10 < A ≤ 25 | 2 |
25 < A ≤ 50 | 1 |
50 < A | 0 |
Un exemple d’indice est : Indice 7 après 500 heures d’exposition au brouillard salin neutre ISO 9227.
Normalement, le nickelage chimique résiste bien à la corrosion lorsque l’épaisseur appropriée est sélectionnée en fonction de l’agressivité de l’environnement dans lequel le composant est utilisé et lorsque les surfaces présentent une bonne finition par usinage mécanique. Il peut varier de 5 à 10 µm d’épaisseur pour les environnements non particulièrement exposés, à 20 µm pour la corrosion modérée, jusqu’à 50 µm pour les environnements agressifs tels que l’environnement marin.
La meilleure résistance à la corrosion sur les alliages de fer et de cuivre est offerte par le nickel chimique haut phosphore Niplate®500 grâce à sa structure amorphe avec une faible porosité, même à des épaisseurs de quelques microns. Le nickel chimique forme la meilleure protection contre la corrosion vers le métal de base lorsqu’il s’agit d’alliages de cuivre, notamment avec le laiton qui est largement utilisé pour les pièces mécaniques. La différence d’électronégativité entre les alliages de Cu-Zn et de Ni-P est presque nulle, ce qui contribue à éviter l’agression de la pièce en laiton nickelé chimiquement. La résistance à la corrosion dépasse dans ce cas 1000 heures en brouillard salin neutre NSS selon la norme ISO 9227.
Pour l’aluminium, le traitement principalement utilisé pour conférer une résistance à la corrosion est l’anodisation. Si en plus de cette caractéristique, on cherche à avoir une surface coulissante à faible rugosité, résistante à l’usure et conductrice, le meilleur revêtement est le Niplate eXtreme. Il s’agit d’un revêtement de nickel chimique spécialement conçu pour améliorer la résistance à la corrosion des alliages d’aluminium. Pour les alliages à haute teneur en silicium, tels que les alliages sous pression, il est recommandé de nous contacter afin de vous proposer la meilleure solution en fonction de l’alliage et de sa composition.