Les revêtements de nickelage chimique sont souvent appliqués sur les pièces mécaniques en raison de leurs propriétés de résistance à la corrosion.
En effet, la couche de nickel chimique présente une résistance chimique élevée et une uniformité d’épaisseur. Ces caractéristiques permettent de former une barrière entre l’alliage de base et l’environnement extérieur, ce qui augmente considérablement la résistance à la corrosion de la pièce.
Ce mécanisme de protection contre la corrosion est complètement différent de celui offert par d’autres revêtements tels que la galvanisation sur le fer. En effet, dans le cas de la galvanisation, la couche de zinc présente sur la surface est sacrificielle par rapport au métal de base. La couche de zinc ne dispose pas de résistance chimique, mais se corrode plus rapidement que l’acier de la base. C’est précisément cette caractéristique, d’être sacrificielle par rapport au fer, qui permet de protéger la base de la corrosion.
Le revêtement de nickel chimique protège de la corrosion en créant une barrière contre l’environnement extérieur. Les points de déclenchement possible de la corrosion sont les zones dans lesquelles le revêtement n’est pas continu.
La continuité et l’intégrité du revêtement, donc le degré de protection contre la corrosion, dépendent de ces facteurs qui peuvent compromettre la continuité de la couche. Les facteurs qui affectent le plus le résultat sont principalement imputables aux opérations effectuées avant le nickelage chimique.
Les principaux facteurs sont les suivants :
- Revêtement
- Type de nickel chimique (moyen, haut phosphore)
- Épaisseur de revêtement
- Pièce à recouvrir
- Alliage métallique de la pièce
- Technologie de production (fusion, moulage, usinage mécanique…)
- Géométrie de la pièce (présence d’arêtes, de filetages)
- Finition de surface et rugosité (surfaces tournées, fraisées, rectifiées, brutes, marbrées, grenaillées…)
Revêtement
Type de nickel chimique
Le type de nickelage chimique, le nickel chimique moyen phosphore ou haut phosphore, influence la résistance à la corrosion. En effet, le nickelage chimique haut phosphore, à épaisseur égale, présente une plus grande uniformité et continuité de la couche.
Ainsi, les pièces recouvertes de nickel chimique haut phosphore Niplate 500 auront, en général, un meilleur comportement à la corrosion que les pièces avec du nickel chimique moyen phosphore Niplate 600.
Épaisseur de revêtement
L’épaisseur du revêtement influence également la résistance à la corrosion. Plus l’épaisseur du revêtement est élevée, plus la couverture, la continuité et l’uniformité du revêtement sont élevées.
L’épaisseur choisie dépend beaucoup de l’application, du type de nickel chimique et du matériau de base de la pièce. En général, lorsqu’une résistance élevée à la corrosion est requise, l’épaisseur du revêtement doit être supérieure à 20 µm dans le cas de pièces en alliage de fer ou d’aluminium. Pour les pièces en alliage de cuivre, une épaisseur de 10 µm est suffisante.
Pièce à recouvrir
Alliage métallique de la pièce
Le comportement à la corrosion dépend fortement de l’alliage métallique recouvert. En effet, sur l’interface entre le métal de base et le revêtement, un couple galvanique se forme entre les deux métaux, ce qui peut créer des phénomènes d’accélération de la corrosion :
- Les alliages de cuivre recouverts de nickel chimique présentent la meilleure résistance à la corrosion. Ces alliages présentent un potentiel de réduction similaire à celui du revêtement et ne forment donc pas de couple galvanique sur l’interface. Les alliages de cuivre recouverts peuvent en toute sécurité dépasser 720 heures de brouillard salin sans corrosion, même avec de faibles épaisseurs de revêtement (environ 10 µm).
- En revanche, les alliages de fer et d’aluminium présentent un potentiel de réduction inférieur à celui du revêtement. Cela forme un couple galvanique qui accélère la corrosion sur l’interface. Dans ce cas, pour avoir une bonne résistance à la corrosion, il est nécessaire d’augmenter l’épaisseur de traitement (généralement supérieure à 20 µm). L’augmentation de l’épaisseur permet d’améliorer la continuité de la couche et donc d’éviter les amorces de corrosion, éliminant ainsi le problème du couple galvanique entre la base et le revêtement.
Technologie de production
Les meilleures performances de résistance à la corrosion sont obtenues pour les pièces produites par usinage mécanique. En effet, l’usinage mécanique, contrairement à la fusion, garantit une surface avec une meilleure finition, une réduction de la rugosité et une absence de porosité.
Les pièces obtenues par fusion, qu’il s’agisse d’aluminium ou de fonte, présentent sur la surface une porosité, des inclusions ou d’autres défauts qui compromettent la continuité de la couche et permettent donc l’amorçage de la corrosion.
Géométrie de la pièce
La géométrie de la pièce peut également influencer la résistance à la corrosion. En effet, la présence d’arêtes vives ou de filetages peut affecter la continuité du revêtement dans ces zones et donc former des zones d’amorçage de la corrosion. Pour améliorer les performances à la corrosion, il est donc conseillé de rayer les arêtes de la pièce lorsque cela est possible.
Finition de surface et rugosité
Le type d’usinage mécanique et la rugosité de la surface influencent de manière significative la résistance à la corrosion (notamment sur les alliages de fer et d’aluminium).
En effet, lorsque la rugosité de surface est élevée (> 1,00 Ra) ou que le matériau présente des déchirures, des arêtes ou des écrasements, il est facile de présenter des amorces de corrosion. Cela est dû au fait que dans ces zones, le revêtement ne peut pas couvrir la surface de manière continue.
Conclusions
Les facteurs qui influencent la résistance à la corrosion sont nombreux et il est difficile de les synthétiser, notamment parce qu’ils sont interconnectés. Le choix des spécifications de traitement dépend également beaucoup de l’application d’utilisation de la pièce.
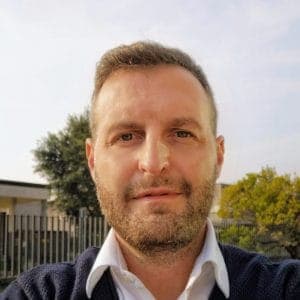