L’énergie propre est devenue une priorité absolue pour les gouvernements et les industries du monde entier, car la réduction des émissions de gaz à effet de serre est devenue essentielle pour limiter l’impact du changement climatique. Dans ce contexte, l’hydrogène apparaît comme une source d’énergie propre prometteuse, notamment pour les véhicules.
Les véhicules à hydrogène offrent des avantages significatifs par rapport aux véhicules électriques, en particulier pour les applications nécessitant le transport de charges lourdes sur de longues distances. Grâce à leur plus grande autonomie et à leur capacité de ravitaillement rapide, ces véhicules sont particulièrement adaptés au transport routier de marchandises sur de longues distances, où les limitations de l’autonomie des batteries et les longs temps de charge constituent des obstacles importants.
Cette caractéristique, associée à la possibilité de produire de l’hydrogène avec des énergies renouvelables au niveau local, fait des véhicules à hydrogène un choix écologique, particulièrement efficace pour réduire les émissions de gaz à effet de serre par rapport aux véhicules à combustibles fossiles, contribuant de manière importante à la réduction de l’impact environnemental dans le secteur des transports.
En résumé, l’hydrogène apparaît comme une source d’énergie propre prometteuse pour les véhicules. Avec la bonne infrastructure de soutien, l’hydrogène pourrait constituer une solution importante pour assurer la transition verte dans les secteurs de l’automobile, des véhicules lourds et industriels.
La nécessité de protéger les pièces mécaniques contre la corrosion et l’usure
La protection des composants du circuit d’hydrogène est d’une importance fondamentale pour assurer la sécurité et la fiabilité des véhicules à hydrogène. Les composants mécaniques du circuit d’hydrogène doivent résister à la corrosion et à l’usure résultant de l’agression des produits chimiques présents sur la route, tels que l’eau, les sels, les hydrocarbures et d’autres polluants environnementaux.
Il est important de souligner que les pressions élevées de l’hydrogène peuvent également causer des problèmes de fuite si les surfaces d’étanchéité des composants du circuit d’hydrogène se corrodent au fil du temps. L’hydrogène est hautement inflammable et toute fuite pourrait créer un environnement explosif. Pour cette raison, la sécurité des véhicules à propulsion à hydrogène dépend également de la capacité des composants du circuit d’hydrogène à résister à la corrosion et à l’usure au cours de la vie du véhicule.
La solution : le nickelage chimique et l’anodisation de l’aluminium comme traitements de surface protecteurs
L’utilisation de traitements de surface peut augmenter la résistance des composants aux contraintes mécaniques et à la corrosion des composants du circuit d’hydrogène, en prolongeant leur durée de vie et en assurant un fonctionnement fiable et sûr des véhicules à hydrogène.
Le nickelage chimique et l’anodisation sont deux traitements de surface qui peuvent être utilisés pour protéger les composants du circuit d’hydrogène contre la corrosion et l’usure.
Le nickelage chimique est un processus de dépôt chimique d’une couche d’alliage de nickel et de phosphore sur la surface du matériau à protéger. Cette couche de nickel offre une protection contre la corrosion et l’usure, en résistant à la corrosion dans les environnements acides et alcalins. En outre, le nickelage chimique peut être utilisé pour protéger contre la corrosion tous les principaux alliages métalliques, notamment les alliages de fer, de cuivre et d’aluminium.
L’anodisation, d’autre part, est un processus électrochimique qui est utilisé pour protéger les alliages d’aluminium contre la corrosion et l’usure. Lors de l’anodisation, une couche d’oxyde d’aluminium est créée sur la surface de l’aluminium. Cette couche d’oxyde d’aluminium agit comme une barrière protectrice contre la corrosion et l’usure et peut être colorée à des fins esthétiques.
En résumé, le nickelage chimique et l’anodisation sont des solutions efficaces pour protéger les composants du circuit d’hydrogène contre la corrosion et l’usure. Ces traitements de surface offrent une protection élevée contre l’agression chimique, ainsi qu’une plus grande résistance mécanique aux contraintes résultant des pressions élevées de l’hydrogène.
Le tableau suivant résume les principales caractéristiques de ces revêtements et le degré de protection indicatif qu’ils peuvent offrir.
Caractéristiques | Nickelage chimique | Anodisation |
---|---|---|
Métaux qui peuvent être recouverts | Alliages d’aluminium Alliages de cuivre Alliages de fer | Alliages d’aluminium |
Résistance à la corrosion dans des environnements à pH neutre | ★★★★☆ sur alliages d’aluminium ★★★★★ sur alliages de cuivre ★★★★☆ sur alliages de fer | ★★★★★ sur alliages d’aluminium |
Résistance à la corrosion dans des environnements à pH légèrement acide | ★★★☆☆ sur alliages d’aluminium ★★★★☆ sur alliages de cuivre ★★★☆☆ sur alliages de fer | ★★☆☆☆ sur alliages d’aluminium |
Résistance à la corrosion dans des environnements à pH légèrement alcalin | ★★★☆☆ sur alliages d’aluminium ★★★★★ sur alliages de cuivre ★★★★☆ sur alliages de fer | ★★☆☆☆ sur alliages d’aluminium |
Résistance à l’usure | ★★★☆☆ sur alliages d’aluminium ★★★★☆ sur alliages de cuivre ★★★★☆ sur alliages de fer | ★★★★★ sur alliages d’aluminium |
Les composants du circuit d’hydrogène qui peuvent bénéficier du nickelage chimique et de l’anodisation
Plaques bipolaires des piles d’électrolyseurs pour la production de H2
Les plaques bipolaires sont des composants essentiels des électrolyseurs car sur leur surface se produit la réaction d’oxydoréduction induite par le courant continu qui transforme l’eau en H2 et O2 gazeux. Ces surfaces doivent être conductrices et doivent résister à la corrosion des solutions aqueuses alcalines ou acides nécessaires à la production de gaz H2 et O2.
Sur ces composants, le nickelage chimique peut offrir des solutions techniquement avantageuses et économiquement valables pour la protection contre la corrosion et le maintien de la conductivité pour certains types d’électrolyseurs (PEM, AEM, AEMWE) où les plaques bipolaires sont en acier au carbone, en acier inoxydable ou en titane.
L’alternative au nickelage chimique est donnée par des revêtements en métaux précieux tels que l’or, le platine, l’iridium ou des revêtements en phase gazeuse tels que les PVD ou les CVD qui ont des coûts beaucoup plus élevés et sont peu praticables à grande échelle. Il est très important que pour le secteur des électrolyseurs qui aura des dimensions mondiales énormes au maximum de son évolution, il soit possible d’utiliser des technologies et des matériaux à haute disponibilité et à faible coût.
Le nickelage chimique a une excellente résistance à la corrosion et peut protéger les plaques bipolaires des réactions de dissolution et d’oxydation qui se produisent sur la cathode et l’anode de la pile ou de la cellule électrolytique.
Notre expertise dans l’application du nickelage chimique sur des plaques bipolaires, combinée à notre capacité à traiter de grands volumes avec efficacité, place Micron srl à l’avant-garde en tant que partenaire pour la production à l’échelle d’électrolyseurs pour l’hydrogène, surtout maintenant que la demande s’accélère.
Micron a développé et produit en interne les formulations pour le nickelage chimique et a perfectionné l’expérience technique nécessaire pour assurer un nickelage chimique efficace sur différents types d’acier inoxydable et de titane.
Pour plus d’informations sur nos services de nickelage chimique et pour savoir comment nous pouvons soutenir votre projet d’électrolyseurs pour la production d’hydrogène, n’hésitez pas à nous contacter. Visitez notre site Web ou contactez-nous directement pour des conseils ou pour demander un devis.
Composants mécaniques du système de stockage et de transfert du H2 dans les véhicules
Les composants du circuit d’hydrogène des véhicules électriques, notamment les corps de vanne, les réducteurs et les pièces des bouteilles, ont souvent besoin d’être protégés contre la corrosion. Le nickelage chimique et l’anodisation peuvent protéger ces composants contre la corrosion et l’usure, en prolongeant leur durée de vie et leur résistance.
Les bouteilles, les corps de vanne et les réducteurs, utilisés pour le stockage, le contrôle du débit et la régulation de la pression de l’hydrogène, peuvent être soumis à la corrosion et à l’usure en raison du frottement mécanique et de l’exposition aux agents atmosphériques et autres agents agressifs. Le nickelage chimique et l’anodisation peuvent protéger les corps de vanne contre la corrosion et l’usure, en augmentant leur résistance et en prolongeant leur durée de vie.
Ces composants sont souvent fabriqués en alliages d’aluminium, un matériau peu coûteux, facilement usinable. Durox a une vaste expérience sur la meilleure façon d’appliquer l’oxydation anodique de l’aluminium pour un résultat qui répond aux exigences les plus strictes en matière de qualité et de fiabilité pour ces composants.
Conclusions : l’importance de la protection de surface
En conclusion, la protection des composants du circuit d’hydrogène par nickelage chimique ou anodisation est une opportunité pour assurer la sécurité et la durée de vie des véhicules à hydrogène. La corrosion et l’usure des composants mécaniques peuvent provoquer des fuites d’hydrogène et potentiellement créer des situations dangereuses. Le nickelage chimique et l’anodisation peuvent améliorer sa durée de vie en garantissant une plus grande sécurité de la chaîne de production et en utilisant l’hydrogène comme source d’énergie propre.
L’hydrogène est une solution importante pour la transition vers un avenir durable et la protection des composants liés à sa production et à son utilisation est un aspect fondamental pour assurer la sécurité et l’efficacité des véhicules à hydrogène dans ce scénario.
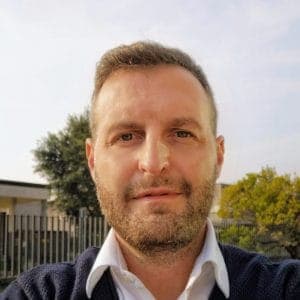