Nella meccanica di precisione, le principali leghe metalliche utilizzate sono quelle di ferro, alluminio e rame, grazie alle loro caratteristiche meccaniche, nonché per reperibilità, economicità e facile lavorabilità.
L’evoluzione del mercato e delle tecnologie ha portato alla necessità di ottenere caratteristiche sempre più elevate, anche sul piano superficiale. Le tre leghe menzionate presentano spesso prestazioni superficiali insufficienti, ad esempio in termini di resistenza alla corrosione o all’usura. Di conseguenza, è molto frequente intervenire con rivestimenti specifici che rispondano a requisiti tecnici e/o estetici.
La nichelatura chimica è il rivestimento che meglio si adatta a componenti di meccanica di precisione, poiché racchiude numerose caratteristiche: uniformità di spessore, elevata durezza, resistenza all’usura ed eccellente resistenza alla corrosione.
Il processo di nichelatura chimica si basa su un’immersione in una soluzione di nichel, innescando una reazione auto-catalitica senza utilizzo di corrente. Sulla superficie del pezzo si forma così una lega nichel-fosforo, frutto della reazione di ossidoriduzione tra lo ione Ni++ (proveniente dal nichel solfato) e lo ione H2PO2- (dal sodio ipofosfito, agente riducente).
Questo processo assicura uno spessore uniforme su tutte le aree, incluse zone interne e geometrie complesse, permettendo il rispetto di tolleranze strette senza isolamenti o rilavorazioni su superfici critiche. Inoltre, rivestire completamente il pezzo garantisce protezione da corrosione e usura anche su superfici interne come fori e sottosquadri.
Nei processi galvanici (o elettrolitici), come la cromatura o la nichelatura elettrolitica, si utilizza invece la corrente elettrica per depositare il metallo. Questo comporta inevitabili maggiore spessore sugli spigoli, e minori spessori nelle aree interne.
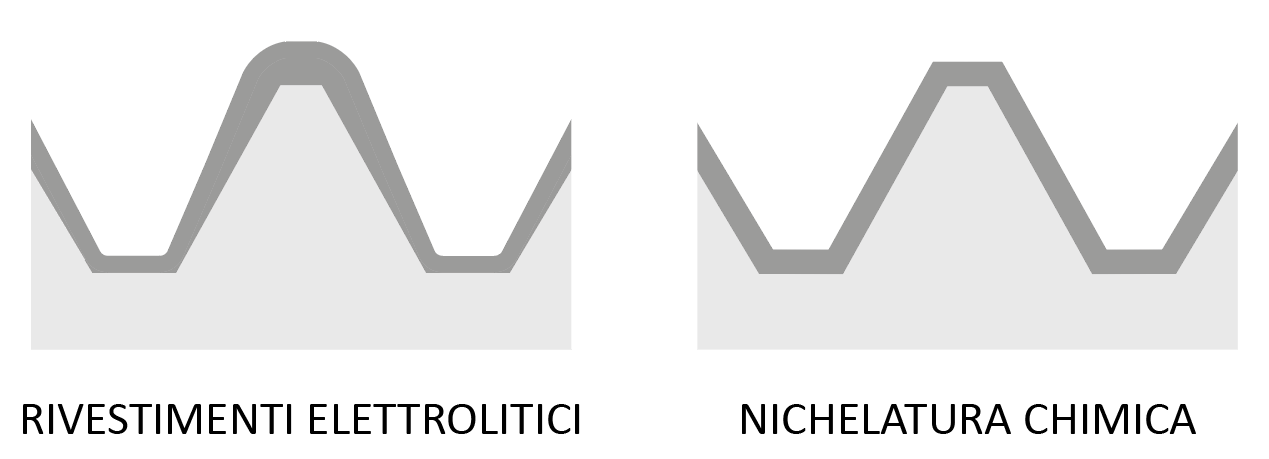
Nichelatura chimica e nichelatura elettrolitica
La nichelatura chimica e quella elettrolitica condividono di fatto solo il metallo nichel, mentre i processi e le caratteristiche superficiali che ne derivano, così come i settori di impiego, sono molto diversi.
La nichelatura elettrolitica si utilizza spesso in ambito decorativo per conferire resistenza alla corrosione e un aspetto metallico argenteo. Generalmente è abbinata a un rivestimento di rame sottostante per favorire l’adesione e ottenere un aspetto lucido e brillante. Ha una durezza media e una resistenza alla corrosione inferiore rispetto a quella chimica.
La nichelatura chimica si preferisce in contesti tecnici in cui siano richieste durezza fino a 1000 HV, resistenza all’usura, riduzione del coefficiente d’attrito ed eccellente resistenza alla corrosione. Può essere applicata su leghe di ferro, alluminio, rame e titanio.
Norme tecniche di riferimento
Le norme tecniche e gli standard internazionali relativi al nichel chimico sono i seguenti:
Norma / Standard | Titolo |
---|---|
ISO 4527 | Metallic coatings - Autocatalytic (electroless) nickel-phosphorus alloy coatings - Specification and test methods |
ASTM B733 | Standard Specification for Autocatalytic (Electroless) Nickel-Phosphorus Coatings on Metal |
MIL-C-26074 | Coatings, Electroless Nickel, Requirement for |
AMS C26074 | Electroless Nickel Coatings |
AMS 2404 | Plating, Electroless Nickel |
AMS 2405 | Electroless Nickel Plating Low Phosphorus |
La norma più diffusa e riconosciuta è la ISO 4527, che definisce requisiti e metodi di prova per rivestimenti nichel-fosforo autocatalitici applicati su substrati metallici.
Tipi di nichel chimico
I rivestimenti si distinguono a seconda della quantità di fosforo presente nella lega:
% di Fosforo | Tipo di nichelatura chimica | Info |
---|---|---|
1-4% P | Nichel chimico basso fosforo | Poco utilizzato industrialmente |
5-9% P | Nichel chimico medio fosforo Niplate 600 | Da preferirsi per la maggiore durezza e resistenza ad usura e per il minore costo |
>10% P | Nichel chimico alto fosforo Niplate 500 | Da preferirsi per la maggiore resistenza a corrosione |
Per incrementare ulteriormente le prestazioni superficiali della nichelatura chimica, sono disponibili rivestimenti con particelle speciali:
- Nichel chimico + PTFE: particelle nanometriche di PTFE vengono co-depositate all’interno dello strato di nichel chimico in concentrazione di 25-35% in volume. Grazie alle proprietà del PTFE, il rivestimento di Niplate 500 PTFE presenta un coefficiente d’attrito molto basso (0,08-0,10) con una elevata resistenza a corrosione, una buona durezza e una eccellente aderenza al metallo base, caratteristiche che mancano nei rivestimenti di PTFE a spruzzo.
- Nichel chimico + SiC: per applicazioni in cui la resistenza all’usura è di primaria importanza, è stato messo a punto il rivestimento composito Niplate 600 SiC . LLe particelle micrometriche di carburo di silicio (SiC), materiale ceramico molto duro, conferiscono al rivestimento eccezionale resistenza all’usura sia abrasiva che adesiva, superando le prestazioni della cromatura.
Aspetto estetico
La nichelatura chimica ha un aspetto metallico brillante, di colore simile all’acciaio inox. Possiede una elevata resistenza all’ossidazione, mantenendo colore e brillantezza a lungo nel tempo.
La morfologia superficiale e la rugosità originarie non vengono modificate in modo significativo dal rivestimento; pertanto, l’aspetto finale rispecchia quello iniziale. Per ottenere una finitura opaca, si possono eseguire sabbiatura, pallinatura o granigliatura.
Il nichel chimico + PTFE ha una colorazione grigio “canna di fucile”.
Il nichel chimico + SiC ha una colorazione grigio chiara.
Leghe metalliche rivestibili
La nichelatura chimica può essere applicata alla maggior parte delle leghe comunemente utilizzate nella meccanica:
- Acciaio al carbonio
- Acciaio inox
- Acciai cementati e temprati
- Leghe di alluminio (da lavorazione o da fusione)
- Leghe di rame, ottone
- Leghe di titanio
Spessore di rivestimento e tolleranza
Lo spessore del rivestimento di nichel chimico è uniforme su tutte le superfici del pezzo. Si utilizzano generalmente spessori compresi tra 5 µm e 50 µm, con tolleranza pari a ±10% (minimo ±2 µm). Gli spessori standard sono:
- 5±2 µm
- 10±2 µm
- 20±2 µm
Per applicazioni gravose, ad esempio in ambiente marino o in condizioni di forte usura, si possono scegliere spessori di 30±3 µm o 50±5 µm, che garantiscono una protezione maggiore in funzione dello spessore.
La scelta dello spessore ideale dipende dai requisiti, dal materiale base e dall’ambiente di esercizio (come usura o aggressività chimica). Micron Srl offre consulenza a progettisti, disegnatori e officine meccaniche per individuare lo spessore più idoneo.
Durezza e trattamenti termici di indurimento
Il rivestimento di nichelatura chimica possiede un’elevata durezza, superiore a quella di molte altre leghe metalliche. Con adeguati trattamenti termici, può raggiungere valori di 1000 HV (69 HRC), superando la durezza di acciai cementati o nitrurati. Ciò conferisce ai componenti rivestiti un’ottima resistenza all’usura, grazie anche al basso coefficiente d’attrito del nichel chimico.
Deidrogenazione
Durante la nichelatura chimica, si verifica una diffusione di idrogeno atomico nel rivestimento e nel substrato metallico. Nei materiali ad alta resistenza, ciò può portare al cosiddetto infragilimento da idrogeno. Tuttavia, rispetto ai processi galvanici (come la cromatura o la nichelatura elettrolitica), la quantità di idrogeno introdotta è inferiore, grazie all’assenza di corrente elettrica. Generalmente si esegue un trattamento termico di deidrogenazione (180°C per 4 ore) per eliminare l’idrogeno e migliorare l’adesione del rivestimento.
Indurimento
I trattamenti termici di indurimento vengono effettuati di norma a 260-280°C per ottenere una durezza intorno a 800 HV e a 340°C per arrivare a circa 1000 HV. Il trattamento termico a 260-280°C può crea una leggera colorazione gialla della superficie dei pezzi a causa di una leggera ossidazione della superficie che avviene a quelle temperature. Il trattamento di indurimento a 340°C, che viene effettuato abitualmente in forno ad aria, provoca una colorazione giallo-blu iridescente sulla superficie dei pezzi. Lo stesso trattamento di indurimento può, in alternativa, essere effettuato in un forno in atmosfera controllata che permette di mantenere l’aspetto metallico del nichel chimico.
Resistenza a corrosione
La nichelatura chimica offre un’eccellente resistenza a corrosione, ma il comportamento varia in base alla lega metallica sottostante:
- Leghe di ferro: la migliore resistenza a corrosione si ha con i trattamenti di zincatura in quanto lo zinco è sacrificale e si corrode per primo, evitando la corrosione del ferro. Il nichel chimico viene scelto in sostituzione alla zincatura quando si richiedono tolleranze strette, protezione anche nelle zone interne, elevata resistenza all’usura o a sostanze leggermente acide o alcaline.
- Leghe di alluminio: il nichel chimico compete con l’anodizzazione, differenziandosi per maggiore durezza superficiale, migliore resistenza chimica in ambienti non neutri, coefficiente di attrito e rugosità più bassi, conducibilità elettrica e rivestimento di tutte le superfici, comprese quelle interne.
- Leghe di rame (ottone): il nichel chimico può fornire una resistenza a corrosione eccellente, arrivando a superare 1000 ore di nebbia salina neutra (NSS) senza segni di corrosione.
Il nichel chimico ha un’ottima resistenza chimica in ambienti neutri o leggermente aggressivi, e mantiene inalterato il proprio aspetto metallico. Resiste bene in presenza di idrocarburi, alcol, soluzioni saline neutre, acidi riducenti diluiti e basi diluite. È meno indicato in presenza di acidi e basi concentrati, specialmente se ossidanti.
Magnetismo
Il nichel chimico medio fosforo (5-9% P) mostra un comportamento ferromagnetico. Al contrario, il nichel chimico ad alto fosforo (>10% P) è amorfo e, in questa condizione, non presenta ferromagnetismo apprezzabile. Tuttavia, se sottoposto a trattamenti termici superiori a circa 250-300 °C, la fase amorfa tende a cristallizzarsi formando composti (ad esempio Ni3P) che conferiscono proprietà ferromagnetiche. Di conseguenza, se l’obiettivo è evitare qualsiasi forma di magnetismo, occorre scegliere un deposito alto fosforo (come Niplate 500) senza eseguire il trattamento di indurimento a temperature tali da innescare la cristallizzazione.
Rugosità
La nichelatura chimica non altera in modo significativo la rugosità superficiale data dalla lavorazione meccanica; i valori restano pressoché invariati rispetto a quelli iniziali.
Rettifica
Alcune particolari applicazioni necessitano di una rettifica dopo rivestimento di nichel chimico, come per esempio gli steli oleodinamici che necessitano di tolleranze strettissime e accoppiamenti precisi.
Il nichel chimico, pur essendo molto duro, si presta a essere rettificato abbastanza facilmente. Viene addirittura preferito il trattamento di indurimento a 800 HV o 1000 HV in quanto risulta migliore la lavorabilità e l’asportabilità del truciolo.
Saldabilità
La nichelatura chimica Niplate si presta facilmente alla saldatura. È molto utilizzato su conduttori in rame allo scopo di evitare l’ossidazione superficiale del rame e permettere una ottima saldabilità di componenti elettronici. Il nichel chimico, oltre a proteggere il rame dalla corrosione, mantiene inalterate le caratteristiche superficiali nel tempo in quanto non si ossida e non si corrode.
REACh e RoHS
I rivestimenti di nichelatura chimica Niplate sono conformi al regolamento REACh e alla direttiva RoHS in quanto non sono presenti sostanze con restrizioni d’uso oltre le concentrazioni massime tollerate e non sono presenti SVHC in quantità superiori a 0,1% in peso.