Differenza tra nichelatura chimica e rivestimenti galvanici
I rivestimenti galvanici (es. cromatura, nichelatura elettrolitica, zincatura, zinco-nichel) vengono depositati mediante l’utilizzo di corrente continua applicata al pezzo, che permette la deposizione del metallo sulla superficie del pezzo da rivestire.
La corrente applicata tende a scaricarsi seguendo il percorso a minore resistenza e di conseguenza lo spessore del rivestimento galvanico risulta maggiore sulle superfici esterne dei pezzi e sugli spigoli, e risulta minore o addirittura mancante sulle cavità interne quando il pezzo rivestito è abbastanza complesso.
La nichelatura chimica è invece un processo di deposizione di una lega di nichel e fosforo che avviene attraverso una reazione chimica di ossido-riduzione, senza l’utilizzo di corrente. La caratteristica principale è quella di rivestire tutte le superfici del pezzo con uno spessore uniforme e calibrato.
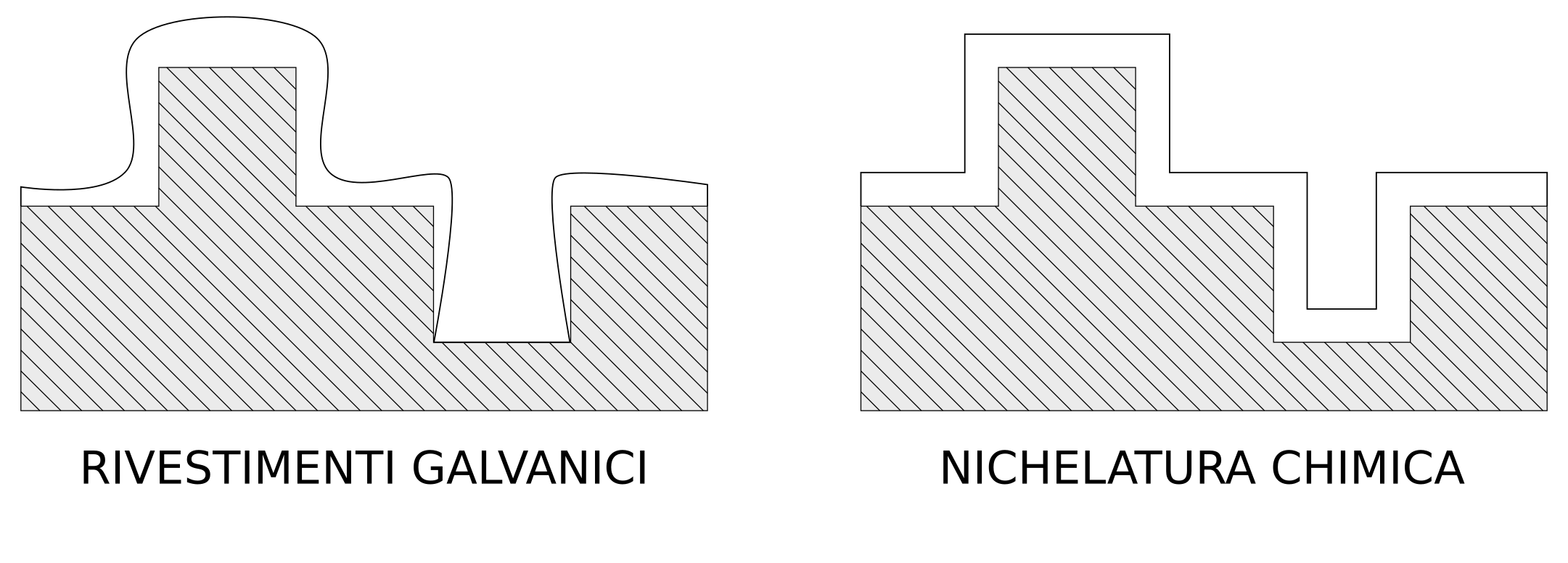
Modalità di protezione dalla corrosione Esistono due tipi di comportamento del rivestimento che influiscono sulla resistenza a corrosione del pezzo rivestito:
- effetto sacrificale
- effetto barriera
EFFETTO SACRIFICALE
E’ la tipica protezione dalla corrosione dei rivestimenti a base di zinco e zinco nichel. Lo zinco ha un valore di potenziale elettrochimico minore del ferro e quindi diventa sacrificale corrodendosi per primo ed evitando la corrosione del ferro. Solo quando lo zinco sarà quasi completamente dissolto, lasciando delle zone scoperte, inizierà la corrosione del ferro, che progredirà velocemente. Un tipico esempio di corrosione sacrificale è l’anodo in magnesio inserito nei bollitori domestici che previene la corrosione dell’acciaio in quanto il magnesio è sacrificale. Un altro esempio sono gli anodi in zinco o magnesio utilizzati sugli scafi delle imbarcazioni. Per tale motivo, per valutare la resistenza a corrosione di pezzi zincati, viene considerato il tempo trascorso prima della comparsa di prodotti di corrosione bianchi (ossido di zinco) e la comparsa di prodotti di corrosione rossi (ossido di ferro). Un esempio di requisito tipico (per la zincatura) di resistenza a corrosione dopo esposizione a nebbia salina neutra secondo ISO 9227 è: 96 ore senza comparsa di corrosione bianca e 168 ore senza comparsa di corrosione rossa.
EFFETTO BARRIERA
La lega di nichel fosforo depositata mediante il processo di nichelatura chimica ha un potenziale elettrochimico maggiore del ferro e dell’alluminio e non è quindi sacrificale rispetto a loro. Agisce come protezione dalla corrosione in quanto crea uno strato barriera che esplica una azione di impermeabilizzazione verso gli agenti aggressivi esterni. La lega di nichel fosforo ha una elevata resistenza chimica e non viene pressoché corrosa da soluzioni saline neutre, soprattutto il Niplate 500 alto fosforo. Per tale motivo, considerando il solo rivestimento, si riescono a raggiungere migliaia di ore di esposizione a nebbia salina senza corrosione. Bisogna però considerare che qualsiasi eventuale imperfezione del rivestimento può generare corrosione del materiale sottostante, anche dopo poco ore di esposizione a nebbia salina. Le cause di tali imperfezioni possono essere molteplici e tra le principali troviamo:
- Porosità del rivestimento dovute al processo stesso di nichelatura o a inclusioni/difetti nel materiale base;
- Superfici lasciate grezze e quindi caratterizzate da difetti di trafila e inclusioni superficiali;
- Grassi, oli e paste di difficile rimozione;
- Spigoli vivi e bave;
Per la nichelatura chimica non ha quindi senso assegnare un limite per la comparsa della ruggine rossa, che può comparire anche dopo poche ore di esposizione laddove il rivestimento presenta un piccolo difetto. Il grosso vantaggio della nichelatura chimica è la capacità di mantenere il substrato protetto anche dopo molte ore di esposizione a nebbia salina, manifestando solamente pochi pitting di corrosione iniziali e di conseguenza un’area di superficie corrosa molto bassa.
Viene quindi solitamente assegnato un Rating di protezione dopo esposizione a nebbia salina per un monte ore deciso dal progettista, come approfondito di seguito.
Valutazione della resistenza a corrosione della nichelatura chimica La resistenza a corrosione di manufatti rivestiti con nichelatura chimica viene valutata abitualmente mediante test di nebbia salina neutra (NSS) secondo le seguenti due specifiche:
Norma | Descrizione |
---|---|
ISO 9227 | Prove di corrosione in atmosfere artificiali - Prove in nebbia salina |
ASTM B117 | Standard Practice for Operating Salt Spray (Fog) Apparatus |
A seguito del test di nebbia salina, la valutazione della resistenza a corrosione viene condotta mediante la specifica UNI EN ISO 10289 - Valutazione di campioni e di manufatti sottoposti a prove di corrosione. Quest’ultima assegna un rating di protezione in funzione dell’area corrosa rispetto all’area esposta a nebbia salina, come riassunto nella seguente tabella:
Area dei difetti A (%) | Rating |
---|---|
Nessun difetto | 10 |
0 < A ≤ 0,1 | 9 |
0,1 < A ≤ 0,25 | 8 |
0,25 < A ≤ 0,5 | 7 |
0,5 < A ≤ 1 | 6 |
1 < A ≤ 2,5 | 5 |
2,5 < A ≤ 5 | 4 |
5 < A ≤ 10 | 3 |
10 < A ≤ 25 | 2 |
25 < A ≤ 50 | 1 |
50 < A | 0 |
Un esempio di rating è: Rating 7 dopo 500 ore di esposizione a nebbia salina neutra ISO 9227.
Normalmente la nichelatura chimica resiste bene alla corrosione quando viene scelto lo spessore adeguato in funzione dell’aggressività dell’ambiente in cui viene utilizzato il componente e quando le superfici hanno una buona finitura da lavorazione meccanica. Si va da spessori di 5-10 µm per ambienti non particolarmente esposti, a 20µm per corrosioni moderate, fino a 50µm per ambienti aggressivi come l’ambiente marino.
La migliore resistenza alla corrosione su leghe di ferro e rame è data dal nichel chimico alto fosforo Niplate®500 grazie alla sua struttura amorfa con bassa porosità anche a spessori di pochi micron. Il nichel chimico crea la migliore protezione dalla corrosione verso il metallo base quando si tratta di leghe di rame, in particolare con l’ottone che è largamente utilizzato per pezzi meccanici. La differenza di elettronegatività tra le leghe di Cu-Zn e di Ni-P è quasi nulla e questo contribuisce ad evitare l’aggressione del pezzo in ottone nichelato chimicamente. La resistenza a corrosione supera in questo caso le 1000 ore in nebbia salina neutra NSS secondo ISO 9227.
Per l’alluminio il trattamento prevalentemente utilizzato per conferire resistenza a corrosione è l’anodizzazione. Se oltre a tale caratteristica si cerca di avere una superficie scorrevole con bassa rugosità, resistente a usura e conduttiva, il migliore rivestimento è il Niplate eXtreme. Si tratta di un rivestimento di nichel chimico studiato appositamente per migliorare la resistenza a corrosione delle leghe di alluminio. Per leghe con alto contenuto di silicio, come leghe da pressofusione, si consiglia di contattarci per potervi proporre la migliore soluzione in funzione della lega e della sua composizione.